The name Liberty Reach may not be synonymous with a company that leads in Industry 4.0 and creates the latest innovations in 3D robotic vision guidance. After all, words like “technology,” “systems,” and “engineering” are nowhere to be found, but don’t let that fool you.
This Dexter, Michigan-based company has more than 400 systems in companies throughout the automotive, manufacturing and aerospace industries. Ford, GM, Stellantis, Toyota, Tesla, Honda, Volkswagen, Lexus, Nissan, BMW, Subaru, Embraer and Joy Global are among the companies that use the patented systems.
“We introduced new [3D] technology that was far superior to what was out there,” said CEO and President Bob Berry. “We made it robust and reliable. The old [2D] technology wasn’t as accurate and was highly susceptible to ambient lighting changes.”
Liberty Reach was founded in 2005 and named for a street in Idaho where founder and current Chief Technical Officer G. Neil Haven owned property.
To the employees, it doesn’t matter what the founder decided to call his business; they are proud of the reputation they helped create.
“We made a name for ourselves in this industry,” Business Development Manager Myron Czubko said.
The source of that pride comes from creating the world’s first robot guidance system to use 3D volumetric sensors with advanced proprietary algorithms to calculate part offsets in six degrees of freedom.
“We put eyes on robots,” Berry said.
Containing sensors, those “eyes” take images — or measurements — and look for irregularities in part placement on an assembly line and guide the robot to the proper place to perform its task. The process takes less than a half second.
“When pieces come down the line, they all might not come down in the same position,” Berry said. “Some might be off a little. 2D imaging wouldn’t necessarily catch the problem, and that could cause delays. Our guidance system catches it and keeps the line moving.”
A unique feature of the system is that it can detect levels of deformation in parts. This allows the user to set a level on how much a part can be deformed before a robot collision may occur. Along with the offset measurement, this deformity level is processed in under one second.
“We have replaced a number of the older technology systems that would take three or four measurements on a part,” Czubko said. “One of the plants we put it in had a dedicated robot with a sensor that would take six measurements around a hood that would take 14 to 15 seconds. We’re doing that in under a second now, so we’re saving them that much cycle time. If that was a bottleneck in the plant, which in this plant it was, the return on investment was a couple of shifts.”
Liberty Reach offers its clients a turnkey system with a 3D sensor, software, industrial PC and cables.
“You don’t have to be an engineer to use the software,” Business Development Manager Jennifer St. John said. “Instead of just one or two people being able to use it, several people can, preventing bottlenecks on the factory floor. When you have more people troubleshooting, it gets downtime over with quickly.”

A look at the technology behind the sensors:
● Sensors use GigE, PoE communications designed for the industrial market.
● Invisible, near-infrared lasers are built in, making the sensors immune to flashing factory lights that cause faults in other vision systems.
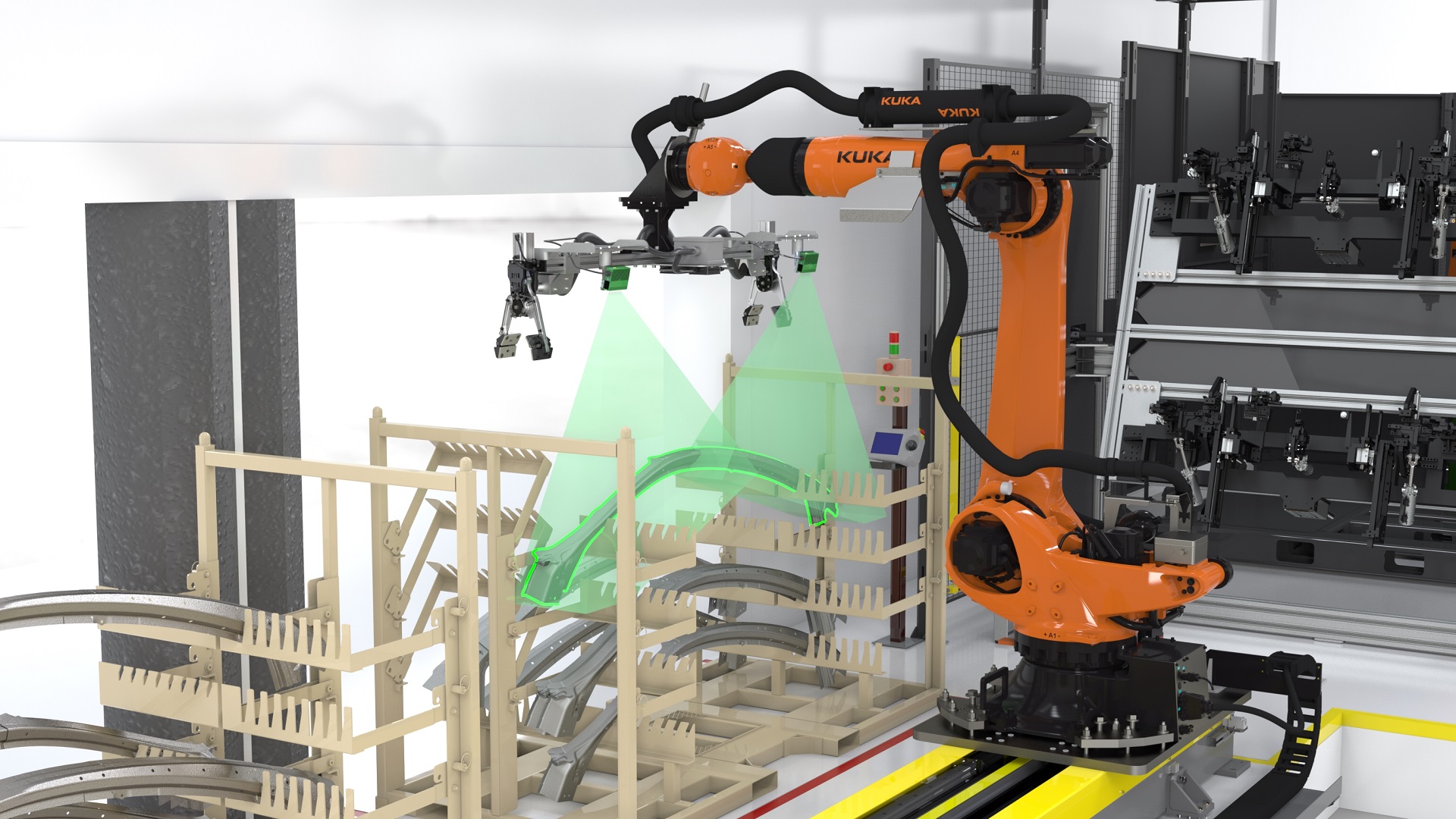
A look at the intelligent software:
● Advanced algorithms developed by Liberty Reach generate an accurate offset in six degrees of freedom in less than one second.
● User-friendly tab-based software is easy to learn and navigate.
● The offset is sent directly to the robot so it can adjust to the unique pose of the workpiece.
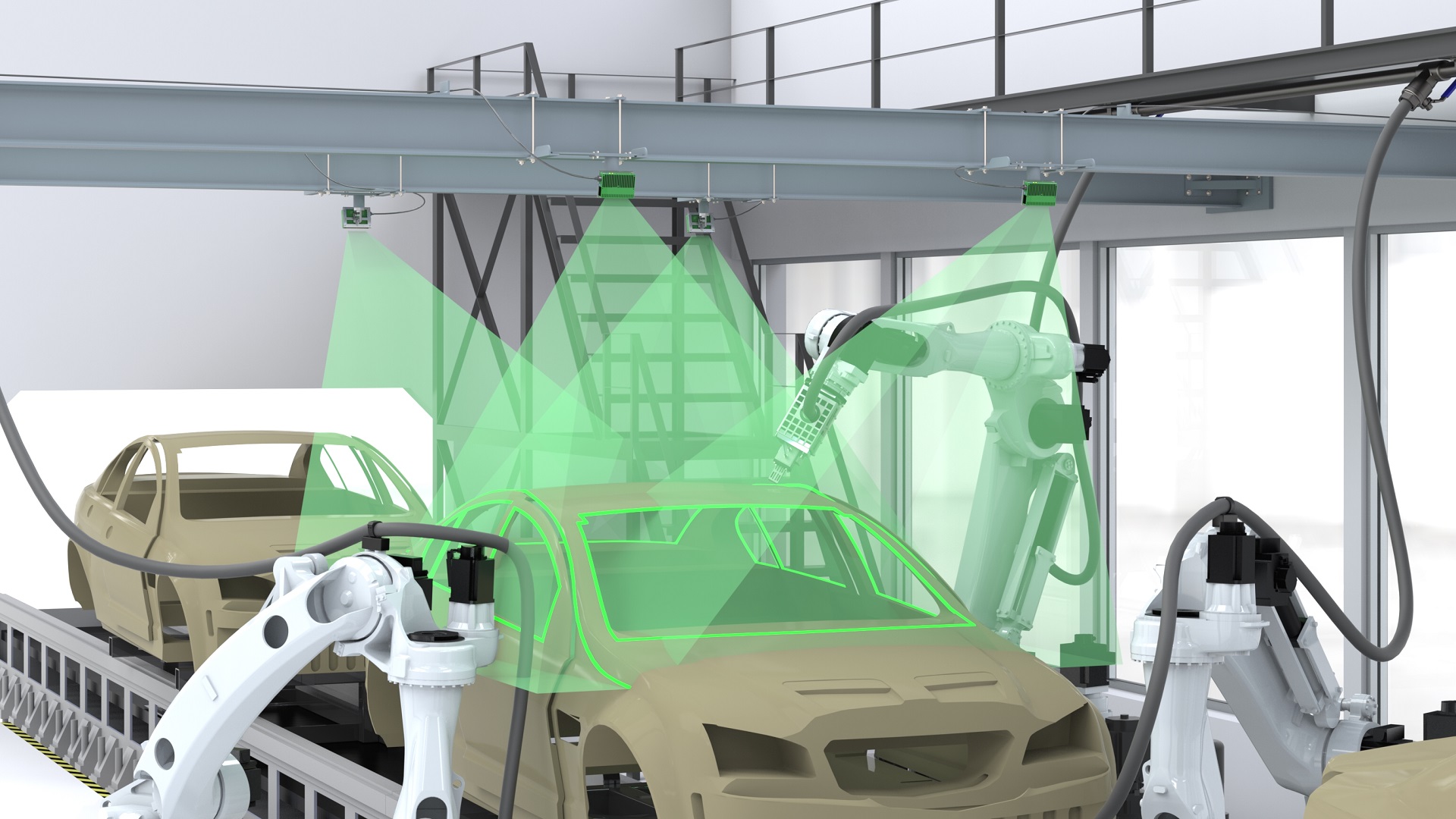
Liberty Reach Created Two Systems Used Mainly in The Automation Industry:
● V-Guide 3D Robot Mounted Vision Guidance is a fast and versatile robot-mounted vision system that utilizes true 3D vision sensors to produce six degrees of freedom offsets in less than one second. V-Guide easily accommodates style additions and model changes with no additional hardware required. Liberty Reach’s proprietary software is easy to learn and navigate. Examples of applications include racking/de-racking, hem sealing and material handling.
● VFix 3D Stationary Vision Guidance uses stationary-mounted sensors to measure six degrees of freedom offsets of large parts or vehicle bodies. Liberty Reach’s proprietary software captures, processes, and sends the data in less than one second, making it the fastest cycle time in the industry. As a result, manufacturers can automate production processes and significantly increase productivity.
Examples of applications include body coating/Hem sealing, material handling, inspection guidance and hood/roof ditch sealing.
After success in the manufacturing industry, the company adapted its system for materials handling and warehouse automation.
“We’ve already gotten some jobs from some pretty high-level brand names that we’re putting into the industry,” Czubko said. “That is a very large market.”
Liberty Reach sent four systems to Saputo, a dairy company in Australia that makes Sargento cheese, to manage cheese boxes.
VPick 3D Vision for pick and place — or de-palletizing — is used for this type of automation. It’s a flexible, dynamic, and intelligent machine vision solution used for automated pick and place in material handling applications. VPick systems consist of Liberty Reach’s proprietary VSx sensor technology and user-friendly software. Together they accurately determine the position, orientation, and size of boxes, bags, and other items, allowing for fast and precise pick and place.
Berry said the company is developing a VPack mixed case palletizing system to take a warehouse’s boxes and place them on pallets or in containers. He added the system would soon be ready to go, and there are plans to increase its distribution.
The Beginning and The Present
Haven worked on robotic motion control and artificial intelligence since the 1980s. He created Liberty Reach in 2005 as a consulting firm before having a revelation.
“Neil saw 3D coming into the market,” Berry said. “He saw techniques that were being applied through the video gaming industry and believed they could be adapted for the industrial automation market. This would be a game-changer in the auto industry.”
In 2011, Haven changed its course from consulting to product development. Czubko joined the company, and Liberty Reach sold its first 3D robotic vision guidance system, which is still in use today.
The company grew from a handful of people working remotely to boasting 37 employees at a facility complete with a testing laboratory.
Revenues have grown on average 25% to 35% year-to-year. And Czubko said the goal is to raise that number to 46% over the next five years. He added there is no external investment, which allows leadership the freedom to make decisions based on what’s best for the company.
“We don’t have to answer to another outside party,” Czubko said, “Our priorities are No. 1 our customers. No. 2 are our employees, and No. 3 are our shareholders.”
That independence allowed Liberty Reach to grow during the beginning of the COVID-19 pandemic in early 2020.
“We put our heads down and focused on strengthening the company,” Director of Product Engineering Wes Tapp said. “We focused on advancing our products. We added staff during the shutdown.”
Management has created a culture where employees get involved with new innovations and develop more efficient systems.
“Most large organizations have silos in which most people are working, and you try to stay in those lanes,” Berry said. “We embrace individuals coming up with new ideas and ways to improve our products and processes. Everybody participates. Everybody contributes. You see the fruits of your labor. It’s important for everyone to have an impact on the organization.”
The leadership stands behind its goal to develop new products by earmarking over 31% of revenue to research and development.
Liberty Reach’s dedication to advancing its position in the industry through a financial commitment to R&D and encouraging employee participation in product development has created a positive work atmosphere.
“This is a great environment to work in,” said V-Guide Product Manager Sarah Coleman, who earned her degree in environmental engineering and has been with the company for five years. “Everybody’s been great. I learned so much about software, robotics and automation.”
Liberty Reach is growing its influence across the technology industry by adhering to its mission of implementing the next generation of automation and, as Berry puts it, continuing to put “eyes” on robots.
Sign up today for a free Essential Membership to Automation Alley to keep your finger on the pulse of digital transformation in Michigan and beyond.