How can the flow of liquids be regulated in zero gravity? How can surgeons have the most precise tools to do life-saving work? The answer to both those questions across wildly different industries involves micro-3D printed parts.
Micro-3D printing, as opposed to traditional 3D printing, involves using additive manufacturing to manufacture parts with micro level features measured in microns rather than millimeters. To put microns in perspective, a human hair is on average 100 microns. Some micro-3D printed parts have dimensions of only a few microns, providing complexity far beyond what subtractive manufacturing methods can offer. In the industrial world, micro-3D printed parts are usually larger, but take advantage of micro level features to add functionality.
On the forefront of this technology in several industries is the German-based MetShape GmbH. Founded in 2019, the company employs a technique known as Lithography-based metal manufacturing (LMM), a sinter-based additive manufacturing technology, especially suitable for producing high precision micro metal parts.
“We see the big advantage of the technology we’ve been using is that you don’t need any post-processing,” CEO and Co-founder Andreas Baum said. “Usually, 3D printing means you print a part, put it on a CNC and machine it to get the right accuracy and surface quality. The part that we print will always be ready to use.”
Regarding surface quality, Baum said that LMM provides near to Metal Injection Molding (MIM) quality without the use of the latter’s pricey tooling process.
“The tolerances we are able to achieve are around 0.5% of the dimension in each direction. LMM has a very good surface quality compared to other 3D printing processes for metals.”
For some customers, wrapping their head around the LMM process after working in traditional manufacturing can be challenging, Baum added.
“Most of the designers start with ‘Here is my metal block, and how do I make my part out of it?’ They don’t think with a 3D printing perspective,” Baum said.
However, one group of unorthodox customers with spacefaring ambitions understood the method was right for them: Students from the International Space Station (ISS) Research Lab Program at Valley Christian High School in San Jose, CA.
According to a press release, students quickly learned traditional manufacturing techniques would not produce a sufficient result, so they looked into the power of Industry 4.0’s additive manufacturing methods to create a part suitable for experimentation on the space station.
Automation Alley member and Southfield-based 3D printing services firm Qualified 3D was contacted by the students to coordinate the production of the part.
This is no easy task: Space is an environment of extremes for all equipment to work in. The part’s material needed to be resistant to vibrations, low temperatures and heat before it could be considered to take off above the atmosphere.
MetShape’s innovative LMM methods and materials provided the solution. Qualified 3D facilitated the transaction.
“Our first reaction was we are super excited for this application,” Baum said. “We contribute to very many interesting applications in the medical and aerospace focus, but we never had the chance to do such a part that can go on a famous station like the ISS.”
The Journey to Space
On Feb. 26, MetShape’s micro-3D printed metal part is scheduled to be launched into space for experimentation on the space station. A Falcon 9 rocket will power the manned-astronaut trip, carrying the SpaceX Dragon capsule Endeavour and four crewmembers to the station.
The part is composed of microlattices with struts as thin as 0.5 mm in diameter to facilitate capillary flow, a dimension nearly impossible to manufacture with known reductive methods.
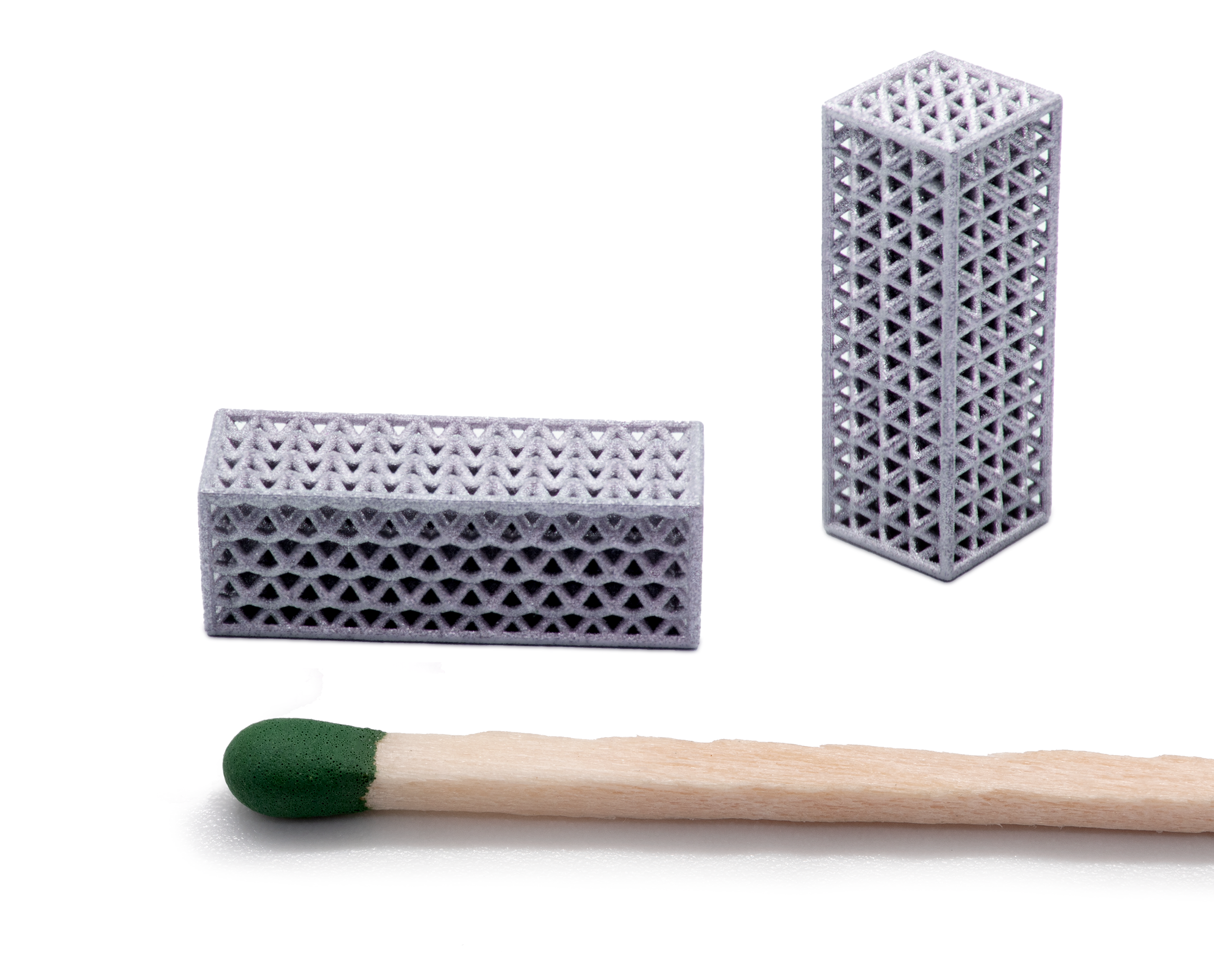
Testing revolves around how liquid flows around these microlattice capillaries. With gravity no longer exerting force on water in space, there is a hope in small and precise capillaries capitalizing on the force of surface tension to provide an alternative method of regulating liquid flow.
“When we saw the part the first time, we thought it is the perfect part for our technology because we are focused on very small and precise parts with very filigreed structures,” Baum said. “The part fulfilled all that so we thought we would be able to produce it.”
The part is made out of Stainless Steel 316L, a highly corrosion resistant steel common in additive manufacturing applications.
“We hope that this part is just the beginning of several lattice structures or any kind of micro parts that are needed for research, or at least for scientific progress on the ISS.”
MetShape is looking at manufacturing similar components for European Space Agency programs as well, Baum added.
Medical Applications
Beyond the realm of testing, MetShape’s technology is changing the way medical manufacturing is done at the ground level. The industry most commonly uses MIM for its precision parts. However, this method has its limits.
“On one hand you need tooling for MIM. The tools are very expensive, especially if you have complex parts,” Baum said. “On the other hand, you may have quite small production volumes for these parts. So, everyone who is manufacturing such parts with an expensive tool and low quantities has a problem because the part will be very expensive.”
This unfavorable cost equation creates the conditions for micro-3D printing to transform the industry.
“The medical industry offers optimal conditions for 3D printing, because it has very complex designs and medium production volumes,” Baum said.
Circumventing the tooling phase not only reduces cost, but allows manufacturers to test and launch their parts faster.
One of MetShape’s customers recently was able to accelerate the validation of robotic surgery component design by testing multiple design iterations at once before validating the final MIM tool design. The part volume was less than 2 mm and would have required a high tooling cost for each iteration.
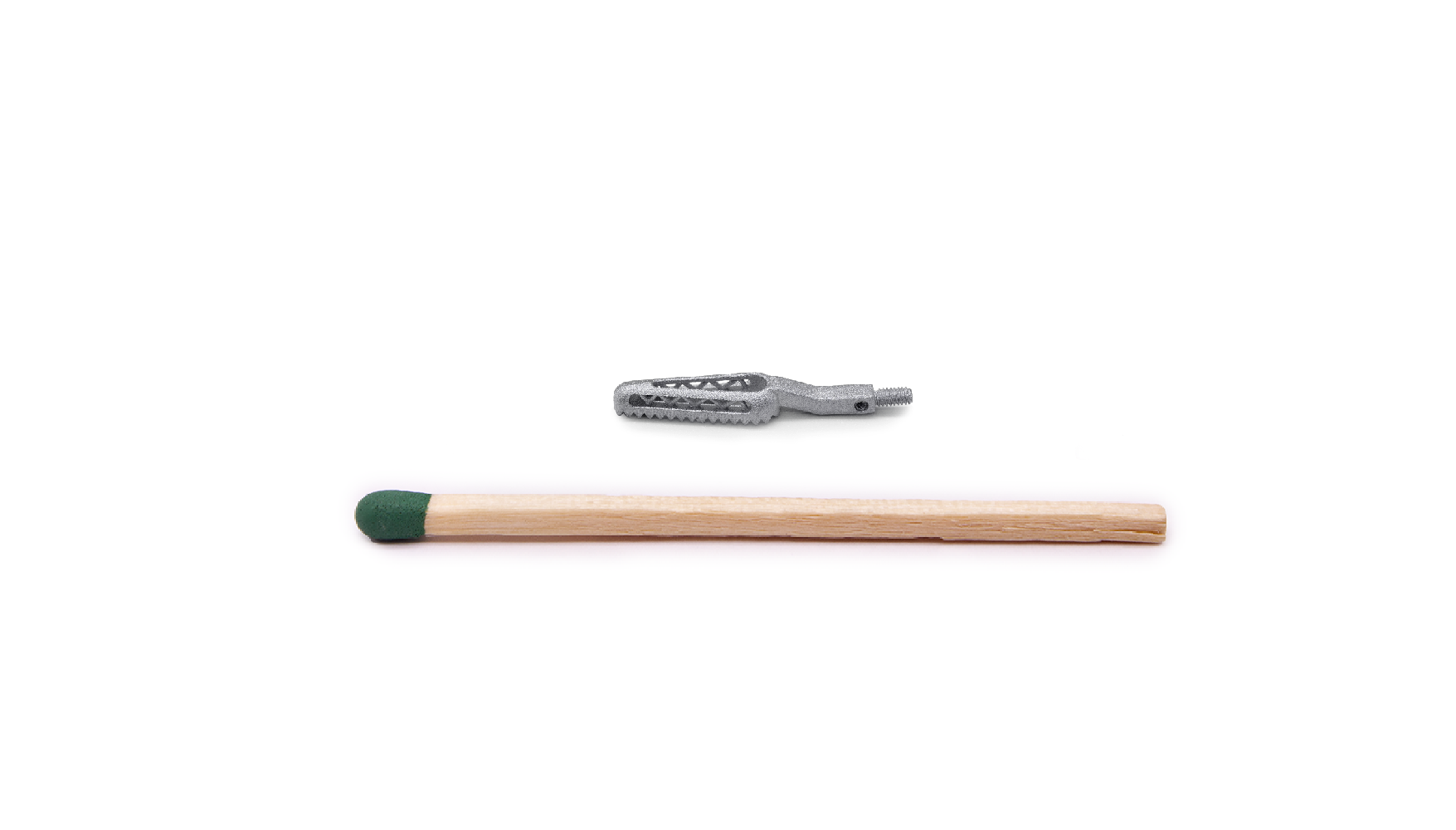
With the additive process making quality parts at a reasonable cost, a greater market shift toward 3D printed parts is possible. Yet, Baum said the biggest barrier to this change is not the capability or cost — it’s the culture of sticking to the status quo.
“Most of our customers are not used to design for additive manufacturing,” Baum said.
“The traditional way of medical device manufacturing involves buying a block of material with certification that the material complies to every norm that should be fulfilled. Then you put it on a machine, mill your part and have the material certification travel with your part.”
But 3D printing is far different for both the customer and company, Baum said.
“Here, we are not only the part manufacturer, but also the material manufacturer. We start with powder and end up with a ready-to-use part.”
A History of Jewelry-Making
The German city of Pforzheim where MetShape is located is renowned for its high-end jewelry and watchmaking, earning it the moniker “Goldstadt” or “Golden City.” Prominent pilot watchmaker Laco calls the city home.
Continuing on this local tradition, jewelry is yet another industry MetShape seeks to operate out of.
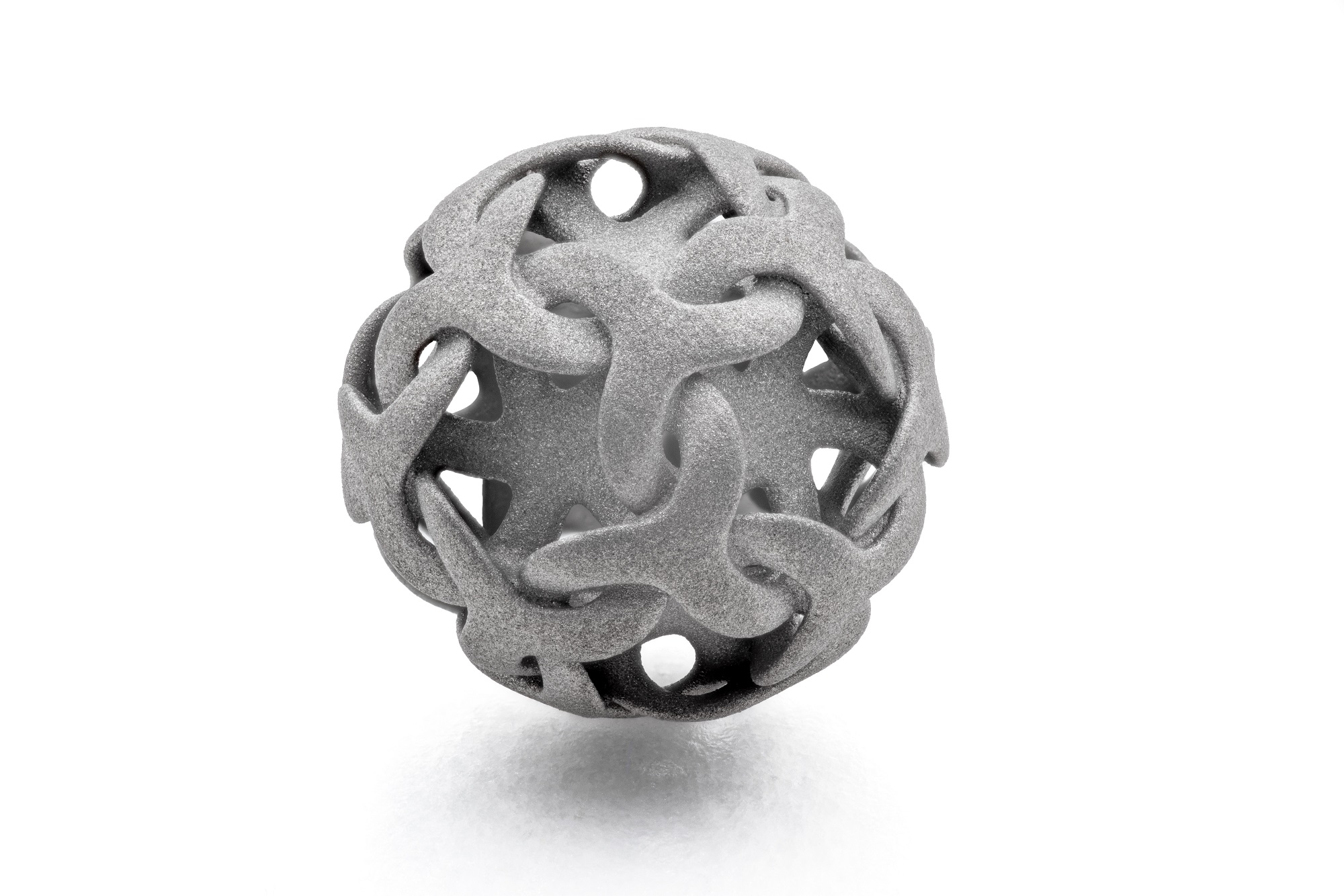
“The jewelry industry is also very interesting for us. We started with watches and had some interesting applications with watch cases, because that is the most interesting thing the designers are changing with watches,” Baum said.
“Some customers work with precious metals and produce very unique jewelry pieces with annual production volumes of only one or two pieces.”
The company is in the process of qualifying gold as a micro-3D printing material for a future project, Baum said.
Looking Ahead
In the year ahead, MetShape plans to continue advancing the micro-3D printing industry from the realm of specialized prototyping to more long term and serial applications.
“This will be a very exciting year for us. We are planning to scale up our production and we’ll try to get the certifications required to manufacture medical devices,” Baum said. “We also have some customers in gold that went with us and want to qualify us as a serial supplier.”
Another focus will be diversifying MetShape’s manufacturing technologies, Baum added.
“As we are a part manufacturer, we do not want to rely on a single production technology. We want to add complementary technologies in house to produce slightly bigger parts as well. We can say our focus on parts will be up to 100 mm.”
Though it takes time to train customers on how to design parts for micro-3D printing, MetShape developed successful training programs. Baum said design training is a large portion of what MetShape does when working with a customer on application cases.
“Up to now, we’ve found a solution for every application,” Baum said.
Sign up today for a free Essential Membership to Automation Alley to keep your finger on the pulse of digital transformation in Michigan and beyond.