The zap of welding and bustle of an open shop floor provided the backdrop for Automation Alley’s latest factory tour and roundtable at Arcstone and SK International’s Digital Manufacturing Center in Wixom, MI. The topic of the event focused on Manufacturing Execution Systems, how they are evolving to suit specific needs, and what challenges they can help companies overcome in the Industry 4.0 era.
Founded in 2005, SK International is a full-service manufacturing company experienced in engineering services and precision manufacturing with proven applications in the automotive, aerospace, and mining industries. The firm features two locations in Michigan as well as two locations abroad in India.
With orders, data, personnel, and projects crisscrossing locations and continents, SK International Vice President and General Manager Steven Remstad said the company needed a capable and high-precision MES to fulfill deliverables across the entirety of SK International’s catalog.
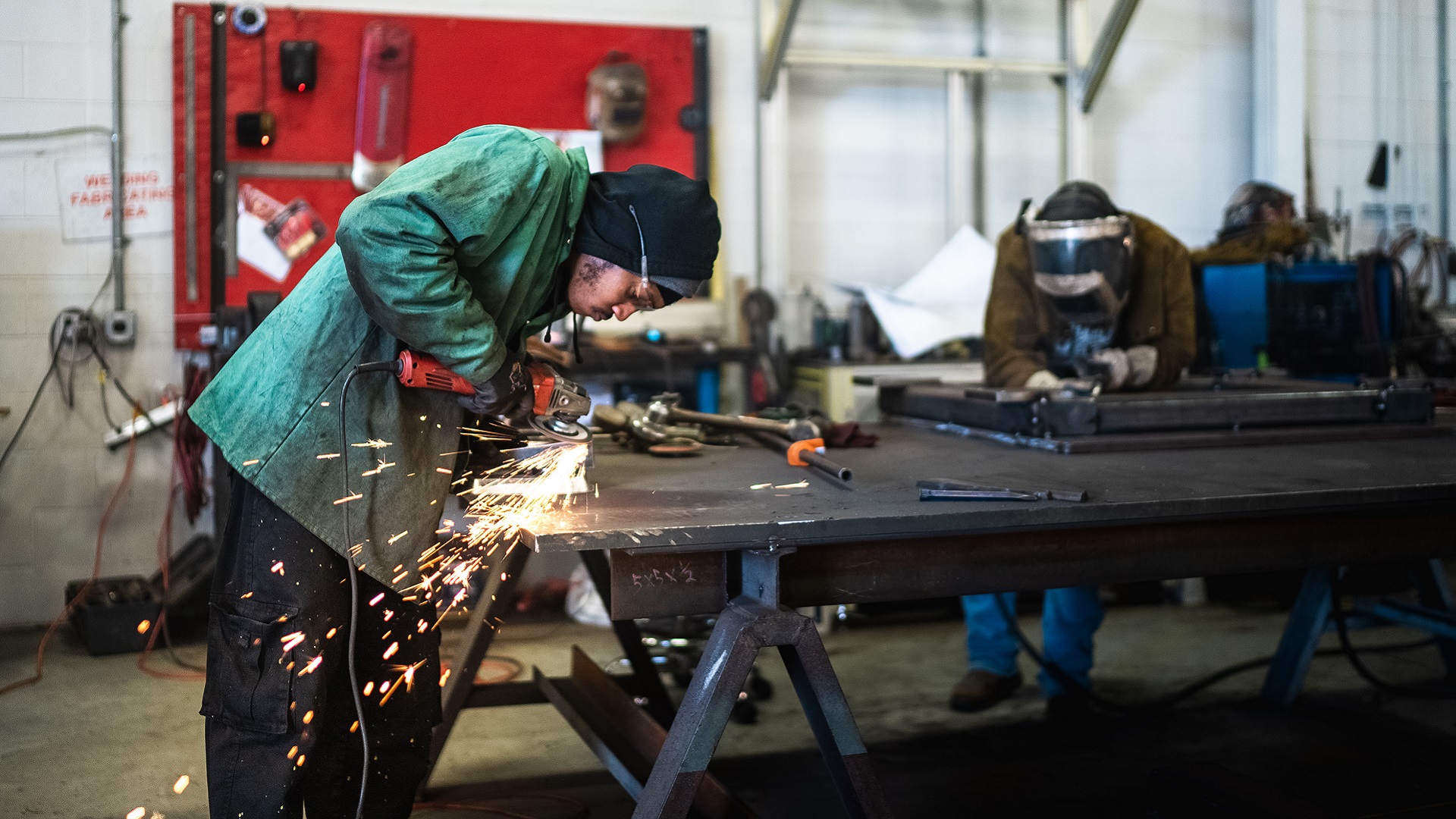
“We were trying to find a different solution than Excel spreadsheets,” Remstad said. “We had tried to develop something in-house and that was marginally successful, but it didn’t have the breadth nor the reliability we were looking for.”
Arcstone’s offering saw immediate applications for SK International, Remstad continued.
“It became something that was a good fit for us due to the size of our organization; plus, what we can do [with it] as we grow as an organization. Our on-time delivery has got better. Our quality level has gotten better. In this case, having that visibility available in a timely fashion makes it a lot easier to meet our deliveries with the quality level our customers are expecting.”
This visibility is on full display in SK International’s Wixom control room. Over five large monitors provide live feedback from multiple phases in SK International’s engineering and manufacturing processes. Staring into the control room, the left side monitors offer real-time quality control and the shop floor. Right side monitors show data from an SK International facility in Hyderabad, India, and engineering phases. The center monitor provides an overview of the real-time status of every job in SK International’s catalog.
This real-time control and feedback from across stations and continents is what the Arcstone MES is designed for, Arcstone CEO Willson Deng said.
“Arcstone has a host of tool sets designed to help the smallest mom-and-pop shops all the way up to multi-billion-dollar Fortune 500 companies. It comes down to the pain points you are trying to solve,” he said.
Among its repertoire, Arcstone offers a multitude of entry points from software monitoring the shop floor to software monitoring the entire sustainability efforts of a large manufacturer and its supply chain, creating a tailor-made MES solution for any interested company.
“We highly focus on the concept of scalability and self-reliability of using the tool — drag and drop, self-configuration, doing everything yourself and making it easy for any user to start going, especially for small to medium businesses that struggle without the internal talent,” Deng said.
For SK International, the company opted for real-time monitoring of workstations on the shop floor with monitors above each station hooked up to the control room and Arcstone’s MES software.
“What you see here in this showcase is not just a solution that is deployed in Detroit, but also a solution that is deployed in Hyderabad,” Deng said. “The beauty of our tools is they are designed so anybody around the world can quickly deploy a full-fledged digital tool that's on the ground, tracking and monitoring all the processes on the shop floor and feeding that up.”
Another component of the Arcstone model is taking preventative steps toward cyber risk and unwanted data collection. Arcstone does not share its users' data, Deng emphasized.
“It is either sitting on-premises on your servers or in a cloud service you own yourself. We make sure that you have full protection and full control over your data, and you can leverage any cybersecurity additions on top of that as you need to so there is no floating data out there in the world. You are managing and controlling everything within your own house.”
Roundtable Roundup
Breaking into three roundtables, over 20 attendees from different disciplines within the Automation Alley ecosystem gathered to talk about MES implementation. Automation Alley provided questions to facilitate dialogue. Here are the key takeaways from the discussion:
What is an MES and how does it differ from an ERP Solution?
● An ERP solution is more of a financial tool while MES is more of a tool for operations.
● An MES functions with work orders while an ERP functions as sales orders.
● An MES provides greater visibility in operations than an ERP solution due to the data it collects.
Where does MES software enable end-to-end visibility, and where does it fit into modern manufacturing processes?
● MES software cuts down on communication errors, which can be prevalent in manufacturing.
● Machine data enables end-to-end connections, and an MES function is the best data collection method for this.
How do we see MES software benefiting small to medium-sized manufacturers, and what are the adoption challenges?
● It provides them with actionable and organized data.
● It will benefit them if personalized.
● Picking the right time to implement an MES is tricky since there is a disruption when changing systems.
● Some small manufacturers do not have the time and money to implement a new MES.
● Implementing an MES adds cyber complexity and cyber risk.
● A company culture change is required.
Is digital transformation via MES simply a method of optimization or is this a necessity in today’s market?
● OEMs are requiring suppliers to be digitized.
● Traceability is a necessity for large customers and an MES will be a necessity.
● In the long run it will be a necessity; however, an MES could hinder a business if implemented incorrectly or rushed.
How can I measure the ROI and the impact of implementing MES?
● It can be measured with the traceability of the MES itself and the better planning the system brings.
● It can be measured with case studies and use cases.
● This metric is tough to build out, especially within a new MES.
● There may be soft savings like employee satisfaction that can be an unknown factor in ROI.
Attendee Insights
At the conclusion of the roundtable discussion, attendees broke into groups to discuss their findings.
Allied Industrial Group Office Coordinator Michele Reynolds said the event helped her envision what MES systems could be like for her operations.
“I want those screens in my office. We want this technology. To see it live and implemented, talking to the people who are using it, is helpful. It is someone that survived the processes and is making it work for them. Also, the roundtable discussion was very good because there were people from all different disciplines from a startup to someone fluent in ERP systems and accounting.”
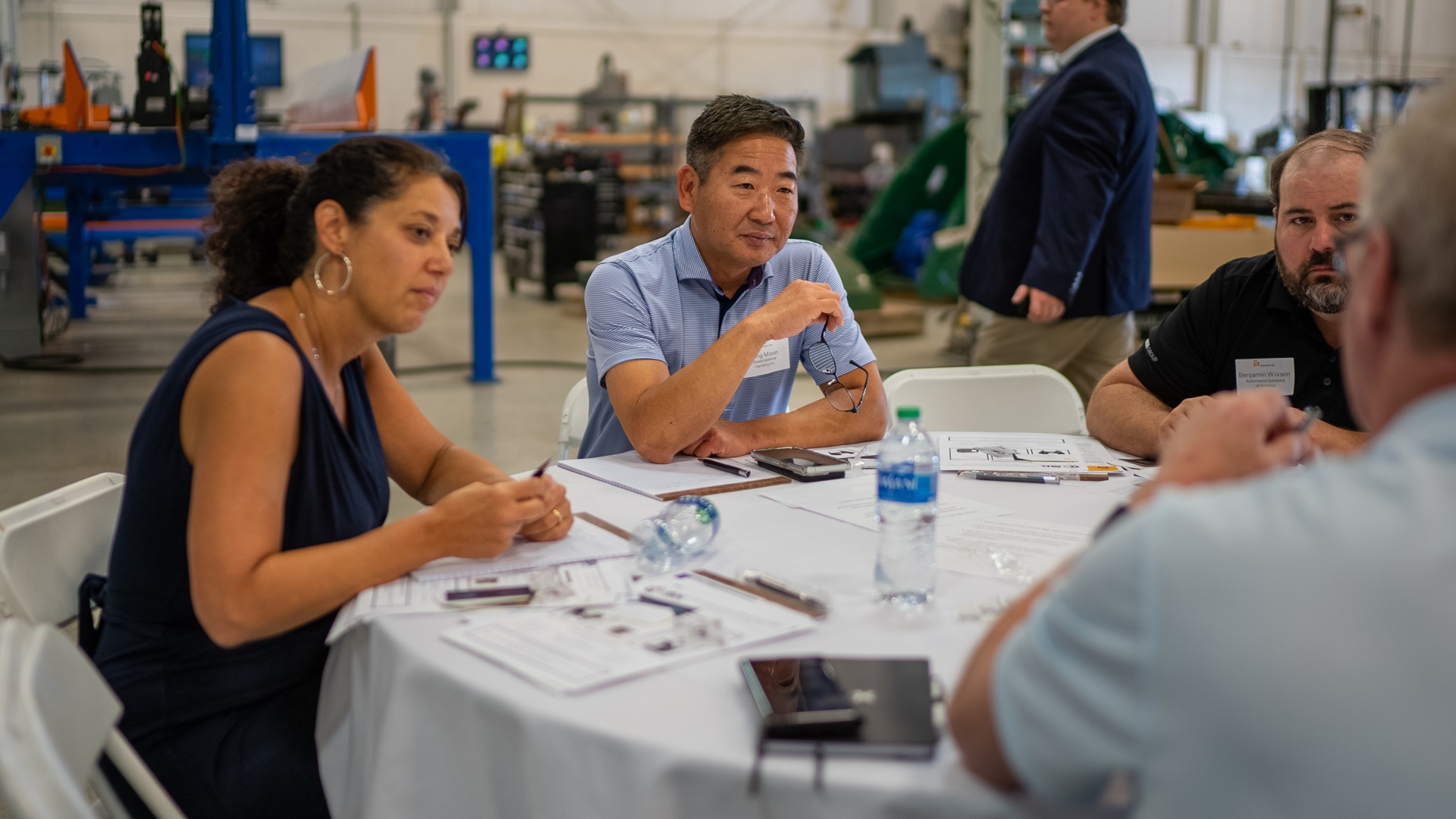
Tarus Products Inc. Vice President of Sales and Marketing George Cook agreed that seeing the capabilities of Arcstone’s MES software first-hand was helpful.
“It is one point to talk about the software, but it is another point to see it in the environment being used with real time data,” Cook said.
“Seeing these things produced in real time on the shop floor was impressive. The way they have integrated this so that everyone in the company so that everyone from the shop floor to the office is operating off the same page is very cool.”
Sign up today for a free Essential Membership to Automation Alley to keep your finger on the pulse of digital transformation in Michigan and beyond.