As the manufacturing world changes, companies need to update equipment, redesign production layouts and plan new production lines. Those processes can be disruptive, but NavVis, an international provider of 3D reality capture and digital factory solutions, has the ability to reduce costs and speed up a factory’s renovation process via the NavVis VLX mobile mapping system.
“We’re ten times faster than anything previously offered in the market,” said NavVis Enterprise Account Executive David Pollock.
He said when an automaker goes from making combustion vehicles to making electric vehicles, they have to transform into EV factories. That process requires taking a 3D snapshot of the space and using that information to design an updated facility.
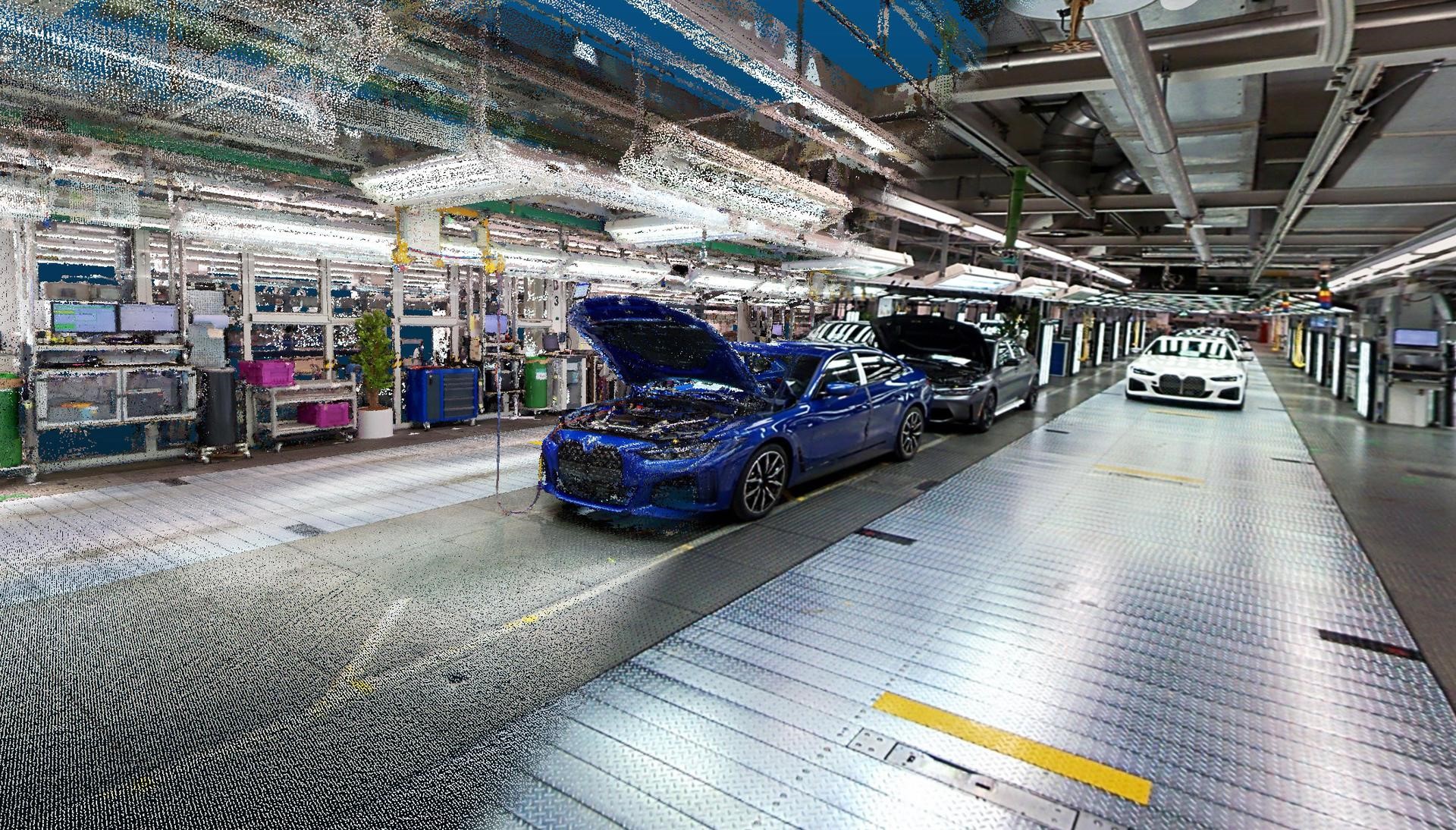
Using old-model 3D capturing systems, which were stationary and needed to be moved to a new location and reset to take more images, took a great deal of time and often left out critical details of the facility. The old process could also cause production lines or entire factories to be closed during the imaging process.
“It was cost prohibitive,” Pollock said. “Now we can create digital factories and look into all areas. Under the old system, there wasn’t time or money budgeted to capture every part of a factory. It left out things like cables, cages, and other infrastructure. This allows you to capture data on all use cases that you traditionally never could.
“Now, what we can create is a digital representation of the factory.”
With mobility, the NavVis VLX makes creating this “digital twin” possible. It’s a 3D imaging-capturing device mounted on a shoulder and waist harness, allowing a person to walk through a facility freely. The collected data is then used to create a 3D panoramic view.
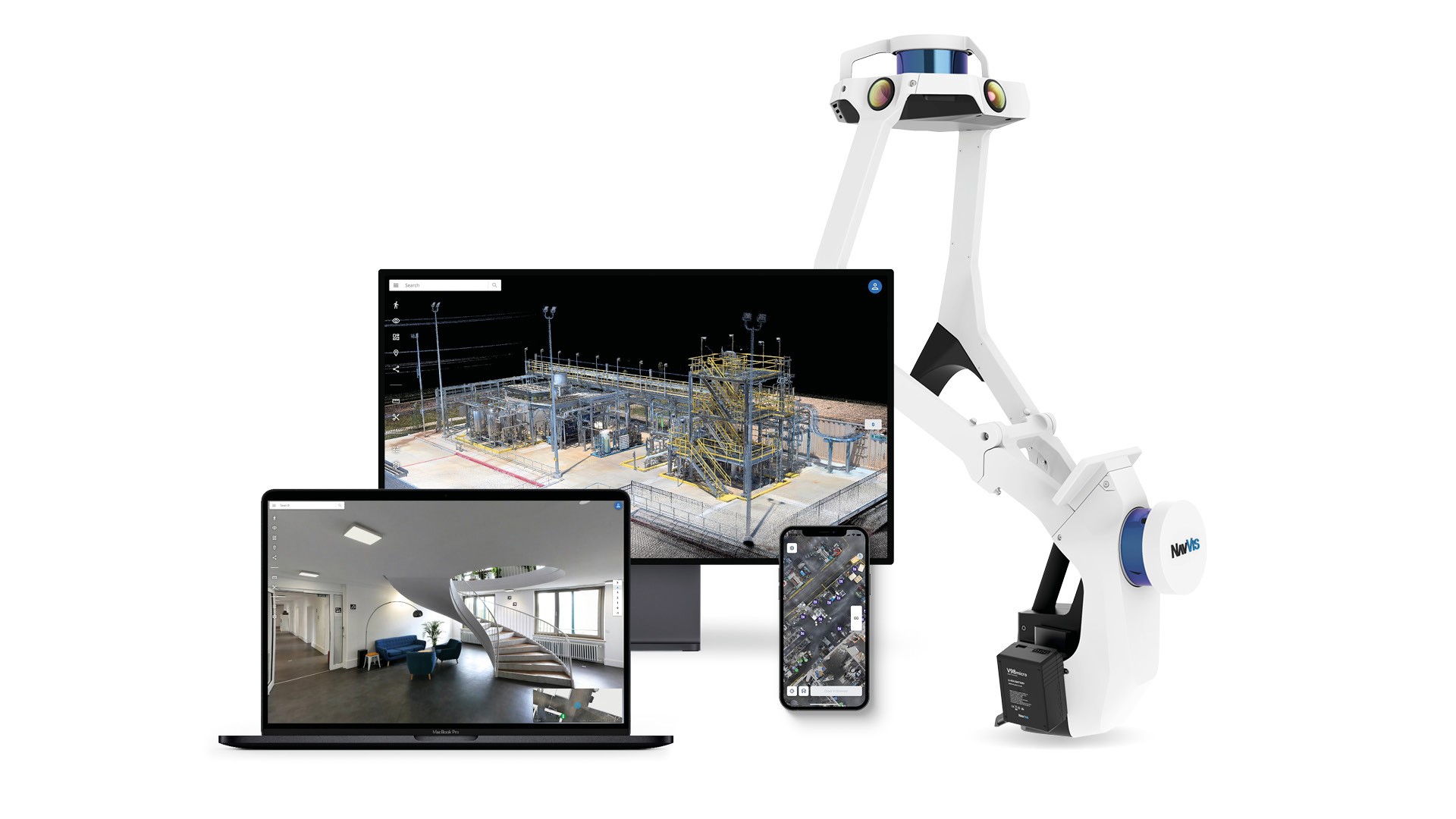
Pollock described the digital creation as something similar to “indoor Google Earth.”
“Google is doing it for outdoors, and we’re doing it for indoors,” he explained. The tools are the same. You can mark it up and make notes. You have virtual access to an entire factory.”
Once the 3D model is complete, clients use NavVis’ proprietary software NavVis IVION Enterprise to interact with their digital factories.
According to the company, the software offers the following benefits:
● Be at any site instantly and easily find information, saving time and reducing travel expenses
● Enhanced industrial engineering productivity through collaboration between stakeholders based on data that's current and reliable
● Directly access and download the relevant 3D scan data from within the browser to compare the as-is conditions with the plan
● Conceptualize and discuss changes together with suppliers and customers within the virtual factory
Connecting the digital factory to the physical factory floor is done through the company’s NavVis IVION Go app (available for iOS and Android.) The app allows users to log observations, issues, and best practices on daily inspections. That information can be shared and discussed with other employees.
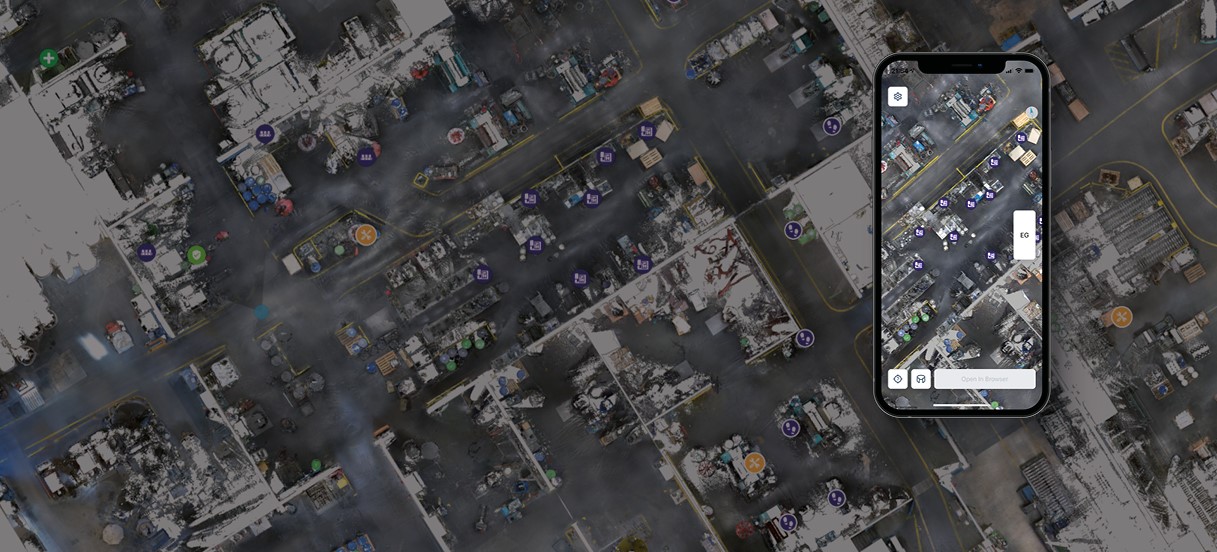
According to the company, the app provides the following benefits:
● Increased team productivity during 5S and Gemba walks with contextual digital notations
● Easy-to-use workflow for collecting improvement ideas
● Reduced maintenance downtime by sharing the precise location of defects and surrounding assets
“It’s like having your factory in your pocket,” Pollock said.
NavVis has clients in North America, Europe, Asia, and Australia; many have facilities worldwide. Its products allow these multinational companies to improve instant collaboration between sites and remote visits with internal teams, suppliers, and contractors, reducing travel expenses and delays in information gathering.
According to NavVis, using 3D digital factories will provide the following:
● A 10-30% reduction of cost for late changes through reduced planning error
● 10-20% greater efficiency through simplified best-practice sharing between different locations
● 20-40% travel cost reduction for industrial engineers due to remotes site visits
NavVis’ comprehensive enterprise product offering, including NavVis VLX mobile mapping system and related software, has benefited automotive original equipment manufacturing (BMW, Daimler); architecture, engineering, and construction; medical device manufacturing; and industrial manufacturing (John Deere, 3M, CNH). NavVis’ products and solutions are also proving to be useful in many interesting outdoor scenarios.
“[The system is] not limited to indoors,” Pollock said. “Big players in the oil and gas industry are all buying our products. Anything to do with virtual reality, augmented reality, and anything surrounding that type of thing, they are buying our products. They need our data to create those worlds. In order to see a 3D world, you need our accurate data.”
Partnering With Automation Alley
NavVis cited several benefits from its Automation Alley partnership, including:
● Executive and Senior Level exposure to OEM and Tier 1 Advanced Manufacturing, Digital Transformation
● Involvement with Industry 4.0 working groups
● Knowledge and Education
● Hosting Events
● Private Meeting Spaces
● Integr8
● Networking
A Look Back
NavVis was founded in 2013, but the idea of a new approach to indoor mapping began with company co-founder and current Chief Technology Officer Dr. Georg Schroth in 2007 while studying at the Stanford University GPS Lab. He later began researching the topic at the Technical University of Munich with Robert Huitl and Sebastian Hilsenbeck. In 2012, Schroth’s close friend Dr. Felix Reinshagen left a position at McKinsey & Company to join the research team. He currently serves as NavVis’ chief executive officer.
“The original vision was to bring ‘digital maps and GPS’ into buildings and thereby close a huge gap of these technologies and services when it came to buildings (and the built environment in general),” according to a company statement. “The name NavVis comes from ‘Navigation by visual means,’ which was the name of the first research project in which Schroth, Robert Huitl, and Sebastian Hilsenbeck started developing the technology of NavVis.”
The startup received some investments and launched the NavVis M3 mobile mapping system and the software solution NavVis IndoorViewer in 2015. In 2018, the NavVis M6 mobile mapping system was launched, followed by the NavVis VLX in 2020. In 2021, NavVis IndoorViewer became NavVis IVION together with the mobile app NavVis IVION Go.
“The journey from prototype to product – both in hardware and software– was a long one, but rich of learnings from mistakes,” said Pollock. “Being a software-driven company, it was hard to maintain focus on clear use cases as people reacted with many ideas to our innovations, creating constant pressure to chase a thousand ideas at once.
“Only once we understood this and got it under control (and started to focus), we were able to pick up speed in iterating on our early product toward better and better product-market fit.”
NavVis, headquartered in Munich, Germany, opened its first international office in New York in 2016 and added a second U.S. office in Los Angeles in 2021. Expansion led to China in 2018, with an office in Shanghai and the United Kingdom in 2022. The company has more than 350 employees.
“We expected to not only disrupt the existing surveying market but also create new markets based on unlocking the power of digital twins in more and more environments,” Pollock said. “Hence, international expansion was always part of the plan so that we can grow into a dominant position in these markets and fully leverage our potential.”
With a solid foundation and a big imprint on the current market, NavVis is growing its global reseller market.
“That’s how we’re expanding,” Pollock said. “Those who used this similar tech are adding our technology to their portfolios.”
Sign up today for a free Essential Membership to Automation Alley to keep your finger on the pulse of digital transformation in Michigan and beyond.