Additive manufacturing reached a critical milestone last night, further proving its viability in the aerospace industry. After eight years of development, additive manufacturing company Relativity Space launched its 3D printed Terran 1 rocket into Earth’s atmosphere, surviving Max Q — a term referring to when forces exert the greatest aerodynamic pressure on a spacecraft.
The rocket was 85% additively manufactured, including its nine Aeon stage-one engines and single Aeon stage-two vacuum engine. Measuring 110 ft. tall and 7.5 ft. wide, the Terran 1 is designed to carry a payload of up to 1,250 kilograms (2756 lbs) into low earth orbit.
However, the rocket’s second-stage vacuum engine failed to ignite during the test launch, cutting the trajectory short of Relativity Space’s goal to reach orbit.
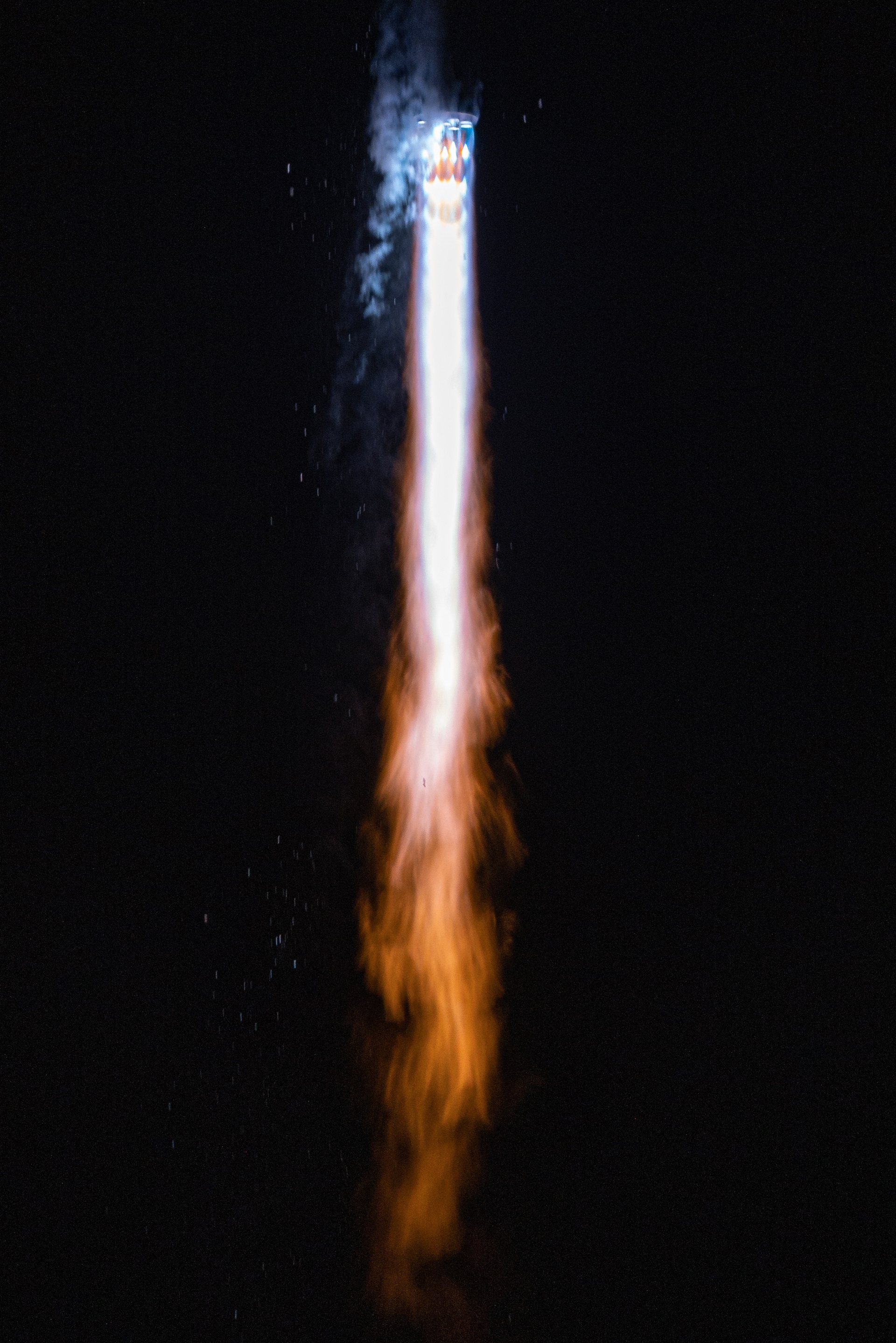
Though the mission fell short of its final goal, the greater proof of concept is plain to see for future launches: According to Relativity Space, its rocket contains less than 1,000 parts and can be additively manufactured in two months with an integrated vertical supply chain. Comparatively, a traditionally manufactured rocket with the same qualities requires a 24 month build time, over 100,000 parts and a global supply chain.
“We are excited to see Relativity Space was successful in demonstrating the viability of 3D printed rockets,” Automation Alley CEO Tom Kelly said. “We are following them closely and wish them great success.”
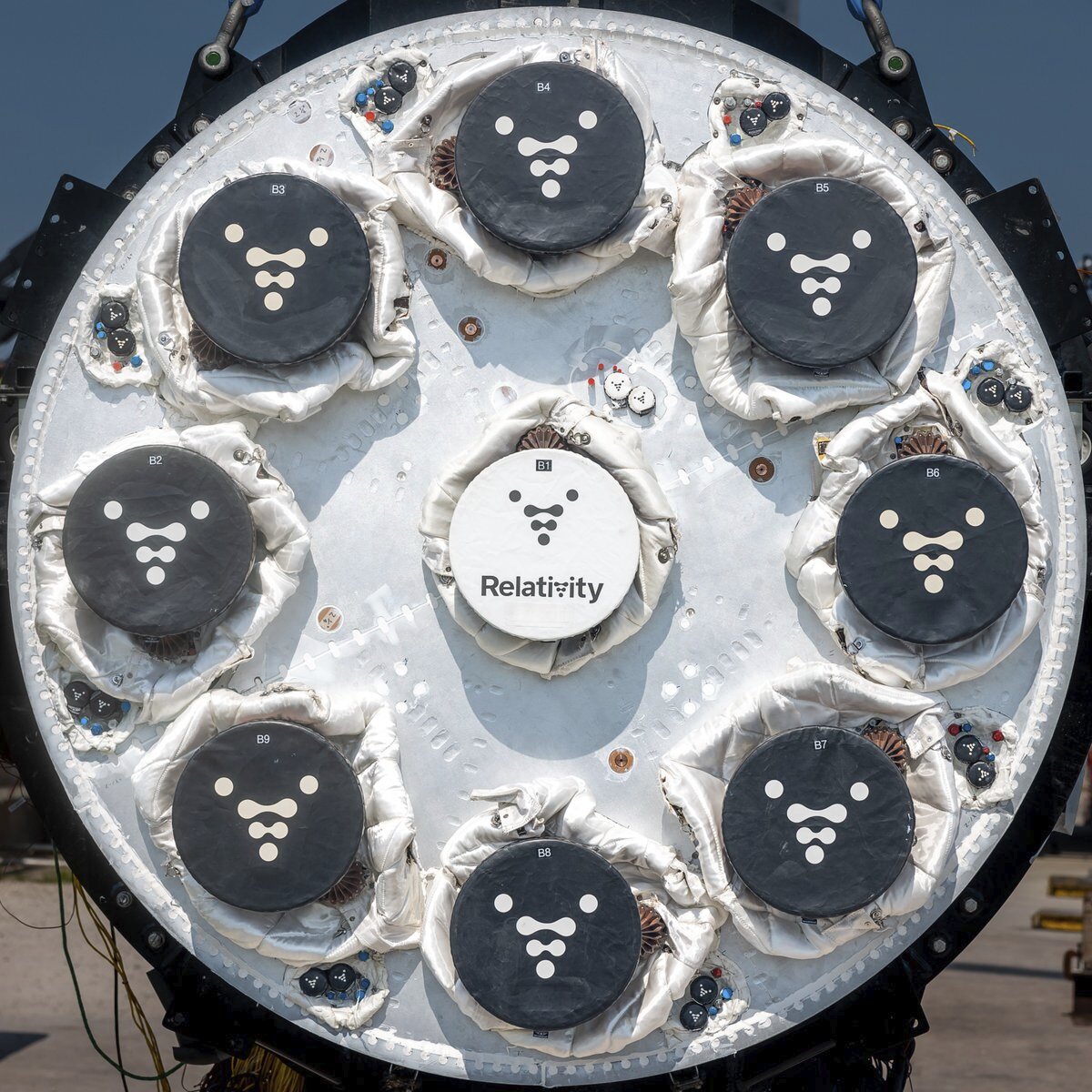
Despite the greater industry implications of the test flight, Relativity Space kept things light with its rocket's nomenclature. The craft wasn’t named after an obscure god from the Greek Pantheon — It is simply named “Good Luck, Have Fun.”
The main components of the rocket were built utilizing Relativity Space’s “Stargate” 3D printer. The machine is capable of additively manufacturing a metallic rocket fuselage in just 60 days out of proprietary in-house printing materials made of high strength alloys.
Alongside 3D printing, the rocket’s construction leveraged other Industry 4.0 technologies such as artificial intelligence, robotics and autonomous manufacturing.
Next on the docket for Relativity Space is testing the Terran R, another additively manufactured rocket designed to be reusable. Automation Alley will cover Relativity Space's next launch when a date is provided.
Sign up today for a free Essential Membership to Automation Alley to keep your finger on the pulse of digital transformation in Michigan and beyond.