Digitization is sweeping manufacturers in Industry 4.0. However, in the race for digital transformation, some may forget that behind every efficiency gain with IoT data is a router powering it, behind every generative AI deployed in design is an ethernet connection, behind every smart camera monitoring the factory floor is a box with an AV feed. These products are the unsung heroes connecting the many facets of the Industry 4.0 world.
Phoenix Contact is a German-based manufacturer of industrial automation, interconnection and interface solutions. Its products are found in factories all over the world from tier one suppliers to small manufacturing machine shops. Celebrating its 100th anniversary in 2023, the centennial company’s founder Hugo Knümann invented the terminal block in 1928. Its technical prowess continues today as it spans the world with offices on every continent but Antarctica.
“We provide the plumbing for Industry 4.0,” Phoenix Contact IIoT senior business development manager Dave Eifert said. “Not only do we sell these in the marketplace, we use our digitalization solutions to help us manufacture them too.”
This puts Phoenix Contact in a unique position as an Industry 4.0 practitioner, Eifert added.
“This makes us walk the walk before we talk the talk: Our products are proven out, born from solving real business and manufacturing problems instead of inventing new technology without any known applicability.”
However, Phoenix Contact’s modus operandi is simple. “We help get data from a sensor startpoint to a database or a cloud,” Eifert explained.
As more manufacturers unlock new potential through software, data collection devices are only expected to grow in importance. The manufacturing industry is one of the largest players in data generation, creating 15 zettabytes of data per year. The World Economic Forum estimates the world will see approximately 463 exabytes of data created daily by 2025. To put that in perspective, one exabyte is equal to one billion gigabytes.
Phoenix contact plans to provide the tools to handle this data surge.
“There is typically a lot of infrastructure that goes into a cloud process. It’s more than a diagram with an arrow pointing from a datapoint to the cloud.”
A simple setup usually entails a humble terminal block, power supply, UPS system, circuit breaker, routers and modems, Eifert said.
Scalability is also important, he added. “We do well with a lot of small and mid-size manufacturers because our solutions are scalable from the low end and up. They are not about top-down digitalization of the entire enterprise or consultant led initiatives.”
Scalable and Low Risk Design
Phoenix Contact’s installation method involves setting up a data gathering system in parallel instead of having it interfering directly in production.
“What we’ve found by automating our own factories, we only need to take a look at 3-5 % of the IO [input-output] that the machine already has on it to do its tasks to get a heartbeat. It is like a stethoscope held up to the machine to get its vital signs,” Eifert said.
“We typically leave the existing control system alone. We most often install the data collection and monitoring system in parallel around it. We can either pick up real-world sensor data through IO, or tap into data the production PLC is already gathering. We then normalize the data, perform any necessary Edge-processing, and send it to databases or applications on premise, in a cloud, or both, depending on need and customer preference. Modern publish-subscribe data models, facilitated by MQTT and brokers are usually a key to the architecture”.
A broker can facilitate connection to a myriad of things — databases, analytics software, Enterprise Resource Planning (ERP) software or a Manufacturing Execution System (MES).
Oftentimes, companies seeking value from one dataset are able to find additional, unexpected value “in the shadow,” of that data. Eifert added.
“Sometimes that can be energy monitoring and savings. Other times it may be anomaly detection for predictive maintenance. But the coolest thing is we have actually found in our own implementations that there may be more to discover outside the primary purpose of collecting data.”
One internal example is in Phoenix Contact’s injection molding systems, involving machines with the highest energy cost. In gathering the data, the team discovered ways to change the energy footprint as intended, Eifert said.
“With a different set of eyes, a data scientist was able to utilize this same data for anomaly detection to see where breakdowns occur. When you have the right data in the right place at the right time with the right people looking at it, you can use it as many times as you’d like to get the most benefit out of it.”
Phoenix Contact’s Solutions in Industry 4.0
Though the company has many applications in Industry 4.0, here are some of Phoenix Contact’s highlighted applications:
Industrial Internet of Things
There are three things that make up installing an IIoT system: a controller like an edge gateway, networking apparatus like fiber optic cables, and the ancillary systems, like a power supply, to make the process work.
“We do all of the above, and over the last 100 years we built up a very good reputation for quality,” Eifert said. “We’ve been vertically integrated for years: We make the machines that make our stuff and make the screws that go into our stuff. Because of that we are able to offer a limited lifetime warranty with most of our components.”
According to Phoenix Contact’s website, its Limited Lifetime Warranty (LLW) program warrants many of our products to be free from defects in workmanship and materials for the lifetime of the product.
Additionally, Phoenix Contact’s products in IIoT go through a gauntlet of testing to stand up to the harshest manufacturing environments.
“When it comes to networking, it is always industrial rated. We test our parts through shock, vibration and temperature extremes, making them stand apart from something you might be able to pick up at Best Buy.”
Another focus of Phoenix Contact’s IIoT products is ergonomics.
“One thing a client brought up to me was our cellular routers had the ability to front load the sim card and memory card. With the other vendor they had to remove it off the back panel to interact with these cards,” Eifert said.
“This sounds like a minor thing but when you have 60 of these units in the field it turns into a major differentiator. We know there will be a technician or control engineer working on this stuff and we design it so it can be easy to handle in the dark and damp environments these men and women work in.”
ClipX Worker Assistance System
Industry 4.0 is often lauded as the convergence of cyber and physical systems. But what does that look like for the modern Industry 4.0 worker? For Phoenix Contact, it looks like its ClipX workstation.
The modular and decentralized system enables tech engineers to access software diagrams, fabricate custom wiring systems and keep in communication with engineers.
“This is about putting power in the hands of the folks doing the designs, making it simple and making it as frictionless as possible,” Eifert said.
With the Clipx station, a machine custom fabricates a wire from an engineer diagram on the screen. The worker is then able to finish the wire with the appropriate endpoint connections with other machines on the table. The process takes mere seconds.
“In the old days you had to pull out a drafting table and a catalog, read up the best you could, then find an instruction sheet for them to send to you. It could take weeks. With Clipx it is all about ease of handling this stuff and building up systems, being able to generate material, wiring diagrams and make the whole cradle to grave project smoother, easier and more error free than the traditional way.”
The ClipX station facilitates people working together, he added.
“It all fits into the umbrella of digitizing all different facets of people’s work life. We want to make it as easy for potential customers to work with us and drive value beyond just the product itself, but the entire experience.”
PLCnext
PLCnext focuses on creating a global ecosystem of developers writing IIoT code and users implementing it. This digital software marketplace enables collaborative, tailored design solutions in real time through cloud integration.
“PLCnext is the biggest thing that I am happy and proud of,” Eifert said.
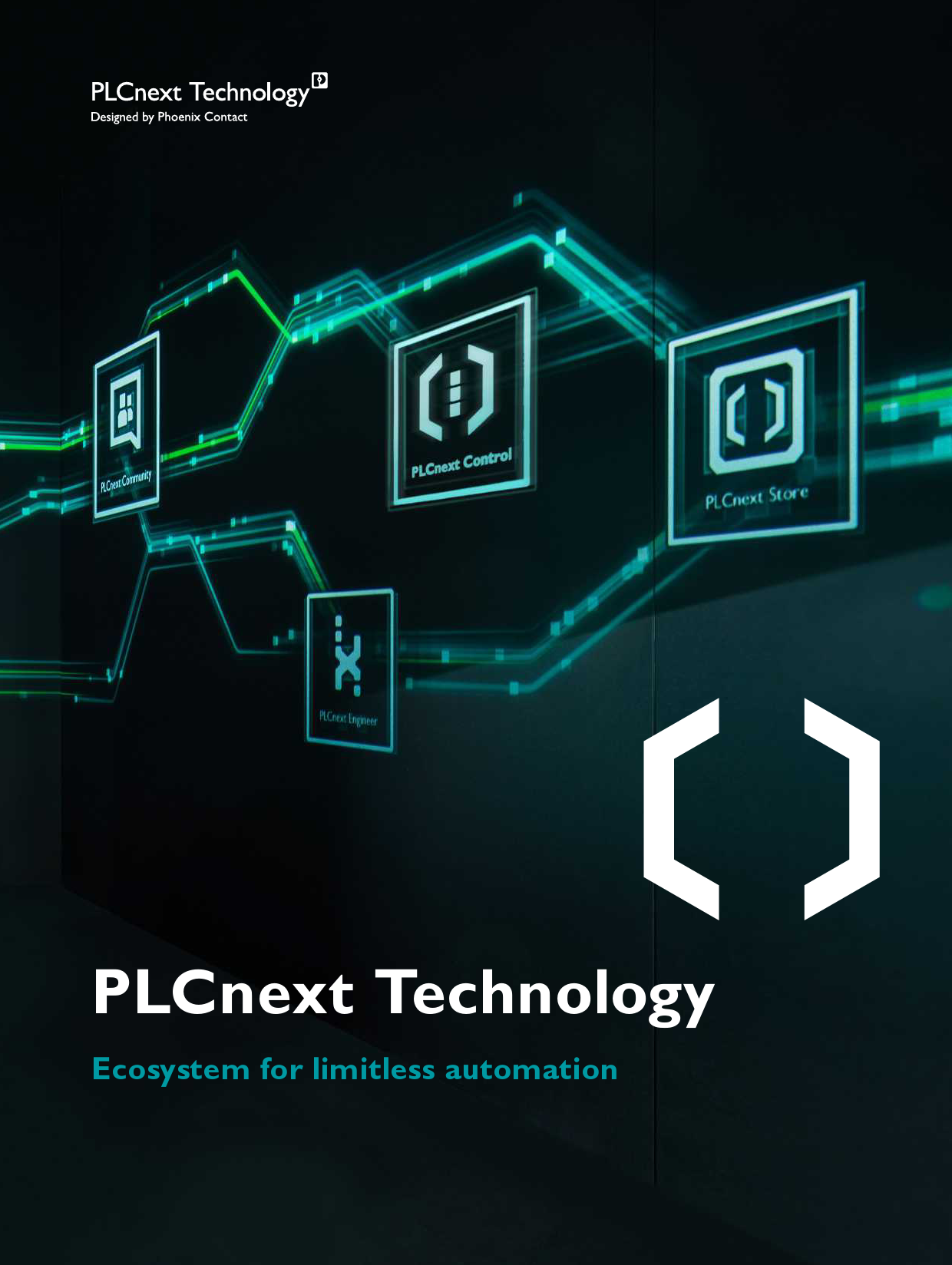
“We can take advantage of the maker mentality. For example if you wrote a program or app and want to sell it on our store, you have to go through a vetting process to make sure there is no malware.
Participants are able to code applications and sell their products, with Phoenix Contact taking a small handling and testing fee.
“People can come up with … let's say a pump efficiency code that can run off our PLC. This can look at cavitation, pump curve efficiencies, and other parameters, and control VFDs and the creator can sell that through our store to the wider market.”
The platform has connectivity to Amazon Web Services (AWS) and Azure as well as Sparkplug-B and MQTT drivers.
“It is really knocking down a lot of walls that were difficult to overcome in the past. It is an exciting time because there are a lot of new ways to do things.”
How to Properly Integrate Industry 4.0 Hardware in a Digital Transformation
Achieving digital transformation as a manufacturer can be harder than it looks on paper. A survey of global manufacturers by the World Economic Forum indicated that 70% of companies that invest in big data analytics, AI, or 3D printing fail to move beyond the pilot phase of development.
Part of why some companies fail in Industry 4.0 adoption could be starting off on the wrong foot, Eifert said.
“IIoT and I4.0 can be buzzword topics that are nebulous and can sound daunting to make that leap,” Eifert said. “Organizations really should get executive buy-in first then immediately take the wide platform down to something manageable in scope.”
Processes and machine IOs are a good starting point.
“Look for something where we can prove an outcome,” Eifert said. “Then apply these tools in a rational way to solve this problem. It may be an iterative thing … but hopefully you can tweak it manually for optimized success. Then once you do, apply this to another machine. Then take the data, open it up to other stakeholders in the organization.”
The future of IIoT is bright and accessible, Eifert added.
“I think we are moving there as an industry where the false promises have been rooted out and people are applying it in a very hands-on way that actually works.”
If interested in getting in touch about Phoenix Contact’s products, feel free to email Dave Eifert at DEifert@phoenixcontact.com.
Sign up today for a free Essential Membership to Automation Alley to keep your finger on the pulse of digital transformation in Michigan and beyond.