The productivity gains promised by Industry 4.0 are, without a doubt, desired objectives for many manufacturers. As more and more organizations start their journey into this smart/digital manufacturing world, we see in our experience that it is frequent for them to incur into a scenario called “PoC limbo”. In this article we will describe how to avoid this type of roadblocks.
Let’s start with a definition: with PoC limbo, sometimes also referred as PoC purgatory, we intend a situation where several Proof of Concept projects are initiated but, because of various reasons, never completed. These projects “fluctuate” in an incomplete status mainly because of lack of communication among the various stakeholders in the organization, which are unable to judge the effectiveness of a solution based on a set of pre-defined metrics. This specific outcome is even more dangerous if we consider the fact that a project “stuck in limbo” is not technically finished, it will not be considered as failed, and therefore its responsible are unable to determine the causes of failure. The only result is this situation is a continuous loss of time and resources that is harder to stop.
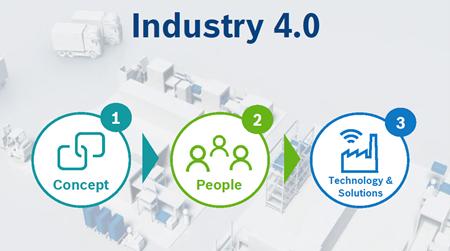
One of the most successful principles in avoiding PoC limbos, is to revert your perspective on your opportunities, rather than using a “technology forward” approach, in our experience we realized that a “bottom-line value backward” strategy is better suited to help all involved parties in prioritize and focus on those pain points that lead to a clear ROI faster.
Defining a Roadmap
In most cases a significant shortcoming is an insufficient roadmap that is predominantly focused on IT only or technology items around IIoT or Industry 4.0. As described in a previous post, the connection to lean manufacturing and a holistic approach is paramount. Hence, a robust roadmap needs to focus and include details of both, the IT and OT topics.
So, how can you accomplish that? There are several methods to choose from and we want to talk about one of the most successful ones – a Kickstarter Workshop.
Within this setting, we want to accomplish a variety of different goals:
- Education on the subject matter
- Creating a Vision and a Mission that the organization can identify with
- Generating competencies and organizational structure required for a seamless and successful transformation
- Change Management specifically to digital transformation
- A clear tie to daily operational pain points
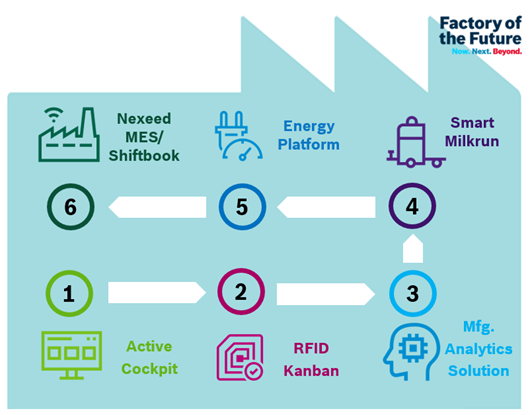
In order to derive a list and prioritization of daily and operational pain points that need to be addressed, one can utilize tools like Rolling Top 5 (RT5) out of the Shainin approach paired with a holistic System-CIP (Continuous Improvement Cycle) to capture not only the “heavy hitters” but to also expose the sum of smaller items of like nature.
Bringing the pain points in line with the newly created Vision and built on a solid lean foundation while applying a change management initiative, the success rate to focus on projects that have the backing of the organization to really solve problems is much higher.
How to Measure Success
So now that your organization has defined a clear path forward for Industry4.0, let's assume that a set of solutions are prioritized, and their implementation is planned. All the stakeholders involved in the project must sit down at the same table and define a set of success metrics, which can vary from group to group: management might have a set of KPIs defining success that are totally different from the manufacturing team metrics.
It is important that every new project implementation must be evaluated at certain determinate stages or milestones, during which the relevant stakeholders can measure how good the solution is performing. This is not only crucial from a performance standpoint, but, for example, it will allow for a new custom solution to pivot its development into a different direction or even kill the project in case it is not delivering any longer on its promises.
A proper IIoT solution evaluation metric is essential to avoid getting stuck in PoC limbo; this approach is valid either in the case of a custom solution, developed in-house, as well as in a system integration scenario.
Change Management
There are different ways and tools available on how you can address this topic. In any case, have a plan on what to expect and how you want to accomplish this. Create for example a simple ADKAR Stakeholder Analysis, apply methods like DISC profiles or Myers-Briggs to understand what support you can get and what roadblocks you will potentially encounter.
Start small, give the users the ability to get familiar with the newly generated data and information. Tie this back to your users’ stories you created during your roadmap development process. Incorporate the new approach in your daily shopfloor management cycles and have the entire team contribute and participate. Gamification can be a good approach to drive acceptance of new data and information.
Once the data and information generated by your new IoT solution is successfully embedded in your daily operation and described via standards, a roll out of the application is now feasible to other areas and the chances that you won’t get stuck in PoC Limbo are looking bright.
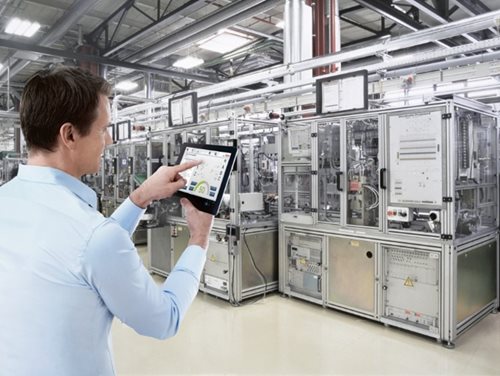
Scaling and Operations
That's it, your organization has successfully designed and implemented a novel Industry4.0 solution which makes management happy, bringing a noticeable efficiency improvement, with contained development costs and with a good UX, helping operators to include it effortlessly in their daily routine. Now it’s time for scaling it. Your solution has been proven to work with a reduced number of machines but scaling it to the whole plant will bring a whole new set of constrains. Payloads and data flows must be optimized for “production”, edge devices and servers must be resized to accommodate for the new computational power required.
This is the phase where proper partner management activities must be setup and kept alive, especially if some of those new solutions were implemented using outsourced engineering service companies and system integrators. IT experts know this well: a house is built to stay the same, a software is built to be changed. Maintaining a software requires constant attentions to every component, for example, dependencies to certain libraries might be broken with a new software release, exposed security flaws might put at risk the whole operation if not patched promptly, just to mention some common scenarios.
As final remark, in order to guarantee long term success of any Industry4.0 activity, an organization must be able to attract and retain talent, necessary condition to guarantee an effective IT & OT bridging and building those cross-functional competencies required in our complex world.