3D printing is transforming the manufacturing landscape, shifting our collective thinking about how products are made. Today, additive manufacturing enables the fabrication of customized parts on demand, with unique chemical properties that enable a wide range of material usages including metals, polymers, and resins. As additive manufacturing continues to advance, manufacturers are faced with important decisions about their future. How will 3D printing compliment current manufacturing technologies? Could the technology eventually be a replacement to traditional subtractive manufacturing techniques? What are the benefits to adoption and what barriers remain? Chapter 2 of Automation Alley’s 2022 Technology in Industry Report places the focus squarely on the business case for additive manufacturing and dives into the mindset shift required, the business model transformations, and the technology considerations that manufactures and the community must address in order to more broadly adopt additive manufacturing.
1. Mindset Shift
Technology has always been the catalyst for disruptive transformation in manufacturing and has enabled both consumers and manufacturers to conceptualize new ideas and bring them to market. 3D printing was first envisioned in 1946, by Murray Leinster, in his short story “Things Pass By,” where he describes drawings being created with a moving arm and molten plastic. It wasn’t until many years later that this technology for additive manufacturing started to become a reality. In the early 1980s, Dr. Hideo Kodama, of the Nagoya Municipal Industrial research institute, was the first to file a patent for a “rapid prototyping device” where lasers were used to cure a polymer. Several years later, this technology was officially patented by Charles Hull, for a stereolithography system, which was approved in 1986, and the company 3D Systems was founded. In the following years, fused filament deposition (FDM), a different form of plastic printing, first came to be when Scott Crump, the cofounder of Stratasys, filed a patent in 1988. It was also during this year that a student Carl Deckard first developed selective laser sintering (SLS) and was able to produce rudimentary pieces of plastic printed together.
Since the 1980s, 3D printing technology has rapidly advanced to what we have available on the market today. Today, additive manufacturing can take a complex digital model, designed by an engineer, and rapidly produce a part layer by layer in a matter of hours with virtually no waste, in a variety of custom materials each with unique properties. (Figure 1) This part can have complex geometric structures, and internal channels, which would be impossible to produce with traditional subtractive processing techniques. But implementing additive manufacturing and generating these types of changes takes a mindset shift, both in how you design for additive, as well as how you manage a company and implement these changes from a business perspective.

Source: https://manufacturing.report/articles/which-additive-manufacturing-process-is-right-for-you
Some of the early adopters to additive manufacturing included aerospace and defense contractors working on functional prototyping, tooling, and other lightweight components. Additive manufacturing as a whole has been also greatly proliferated among hobbyist, while adoption to manufacturing has been slower due to several barriers including lack of technology awareness, cost of entry and a reluctance to replace legacy systems. However, additive manufacturing is gaining traction in the mainstream manufacturing community, with the global additive manufacturing market estimated to reach $76.16 billion by 2030, growing at a CAGR of 20.8%, according to a new report by Research And Markets.
In today’s manufacturing market, we are past a tipping point and are now seeing a slow increase in the usage of additive manufacturing for mass production. Some of these changes are implemented through the initial modeling of an idea during the design stage, and now, as more advanced materials have been developed, and systems with a higher accuracy and higher reproducibility capable of printing materials each with unique properties have been developed, so has their applications and usage. A 2018 JABIL survey reported that an estimated 94% of automotive industry stakeholders are expanding capabilities using 3D printing. Companies such as General Motors, Ford Motor Company, Porsche, BMW and Volkswagen Europa are actively using additive manufacturing. Examples include custom cabin air-duct work in a car for the HVAC system and end-of-arm tooling for robotics and jigs for alignment during manufacturing. One famous example of additive manufacturing showcased is GE’s implementation and optimization of metal additive manufacturing includes finetuning parameters to produce a fuel nozzle for their jet engine propulsion system. The combination of parts showcased a mindset shift, where, a redesigned assembly was produced, combining 20 pieces into a single component, reducing the weight by 25%. This innovating design is saving airline customers thousands of dollars in fuel costs, due to increased efficiency and decreased mass.
Designing for additive manufacturing is a mindset shift that engineers, architects and planners must make in order to fully realize the potential for what 3D printing can do. (Figure 2) It requires becoming familiar with the material availability that is on the market, and the properties that can be leveraged by combining unique materials for the right job. It also means becoming familiar with additive manufacturing hardware and both its benefits and limitations. The power of fully embracing this technology allows for the full integration of a part, and its optimization. It means that you can design a part, computationally model the part, and understand the stress-strain dynamics, react, make changes, and then have the computationally optimized part manufactured exactly how it was designed. This not only shortens the product development lifecycle, but also allows designers to be smarter with the parts that are engineered.
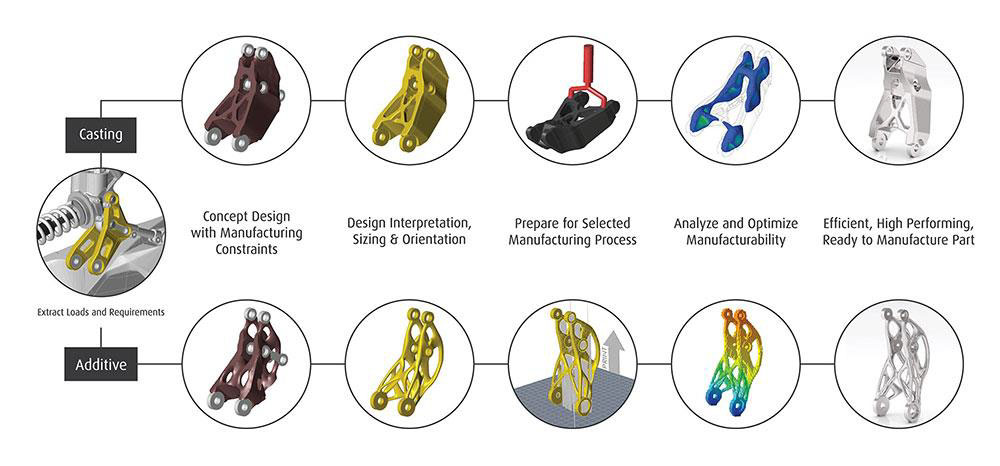
In order to get to this point, however, two important changes must occur. First, at an education level, programs must be designed around additive manufacturing both at the primary and colligate level. This will allow students to have the opportunity to learn how to think critically about the whole design process, and not design based on available components but generate innovative designs for 3D printing. Second, in the workplace, leadership must begin to develop business models that support 3D printing and create workplace cultures that embrace technology change. We need leaders who are forward thinking and think outside the box, ones that are willing to change with technology as it advances, and accept new technologies. It is well known in industry that there are three key categories of business adoption: the advanced adopter, whom takes great risk, and is at the cutting edge of new technologies. They seek innovation, and work to move and leverage new opportunities created by technology. The second is the average adopter. They are slower to adopt but are paying attention to innovation. This is a broad category, where those that adopt early may have contact with innovators, but are waiting for the technology to settle and be tested. Those that adopt slightly later in this category are more skeptical about innovation and waiting for the technology to mature before taking a financial risk. Finally, the straggler adopters are those that adopt last, and generally do not like change. They want to continue using stable and proven technologies. They change because they have to, and rely on older technologies. Additive manufacturing has now matured into a reliable technology with great equipment and software options for manufactures creating systems capable of high precision and accuracy that are highly reproducible and, thus, should be ready for adoption by all.
Yet, many fear that additive manufacturing will replace factory workers, especially at established injection molding and subtractive manufacturing facilities. This couldn’t be farther from reality, where additive manufacturing is another tool in a designers/manufactures arsenal of machinery to produce a part or product for an intended purpose. Additive manufacturing is not a replacement technique for modern day manufacturing, as it cannot produce thousands of parts at a time. (Figure 3) Molding machinery and tooling are an expensive, and time-consuming investment. Where 3D printing serves to operate is the versatility and customization of a part that can be produced. Through building a toolset of additive manufacturing machinery— whether it be a single printer in an office, or a fleet of machines on a production floor—additive manufacturing is a worthwhile complementary toolset to traditional manufacturing.
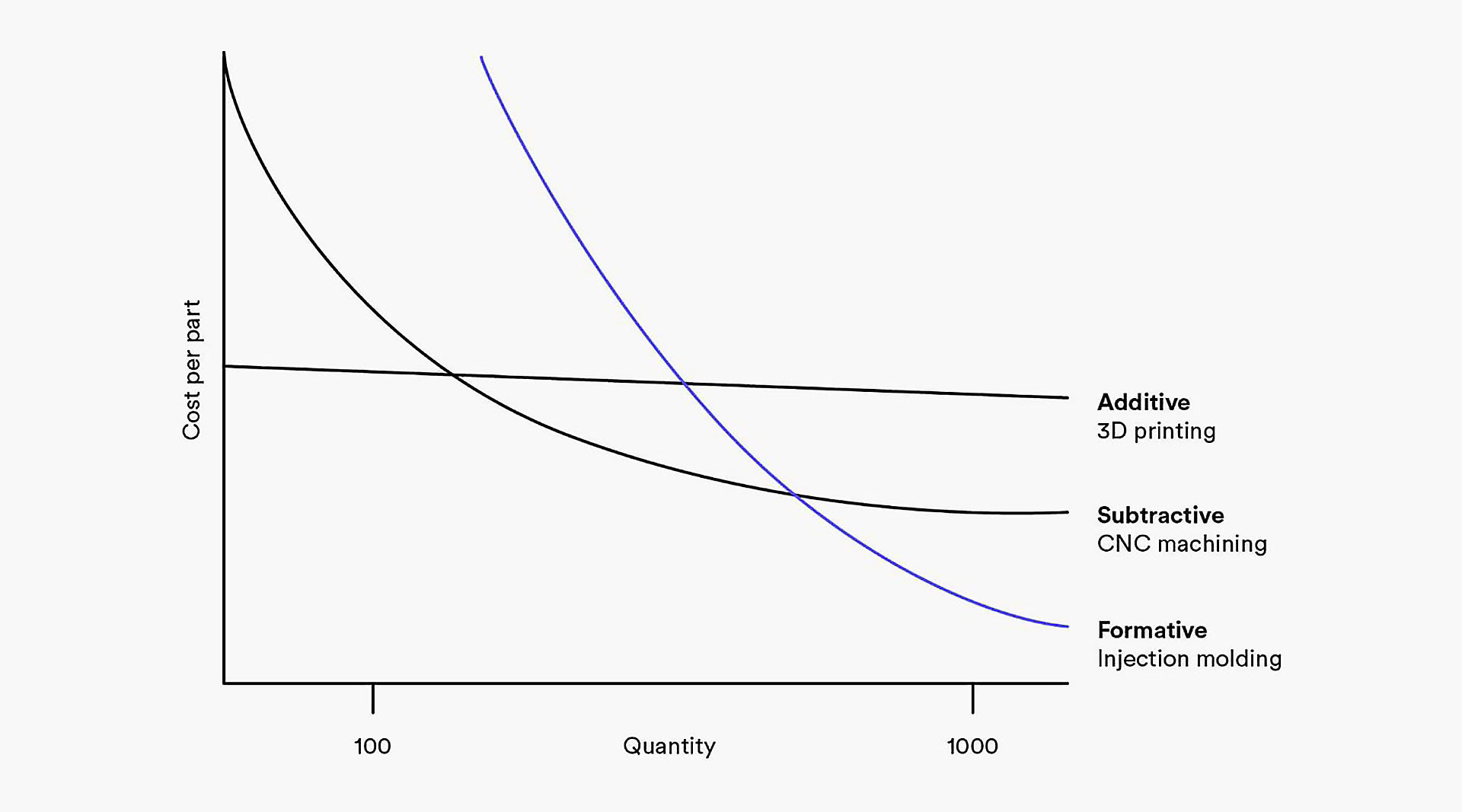
When considering additive manufacturing as a complimentary toolset, it is important to remember that 3D printing as a means of mass production is a lower volume method, but it allows for the complete customization of the part. Additionally, it can be utilized as end-of-arm tooling, and complementary to high-volume production machinery. With that, it becomes necessary to always be a student, and to learn what the current available materials are, and their limitations and usage with additive manufacturing. Thus, it becomes imperative for continuing education, and to never fear new ideas that continue to drive innovation. One idea to consider is to add additive manufacturing systems and enable access to these to employees and personal that are outside the production floor, and to see how they can innovate their workflow.
2. Business Model
When businesses and society effectively screeched to a halt in 2020 as a result of the COVID-19 pandemic, 3D printing proved to be an extremely valuable technology for rapidly producing needed products including life-saving medical equipment and PPE. But the pandemic also had negative impacts on the additive manufacturing economy as lockdowns and limitations hampered the manufacture of additive manufacturing printers. These restrictions and lockdowns slowed the market’s expansion significantly.
As we come out of the worst of the pandemic, the rise of hobbyist print farms has been a fascinating story to watch, with hobbyists creating small models and rapidly manufacturing and selling them. This can be as simple as a trinket with custom colors, or as complex as a commissioned bracket and customized piece for a local company. These hobbyist print farms are not alone in their rise, as we are also seeing growth on an industrial level. To better service companies, there are now print-on-demand manufacture suppliers, such as Azoth and Xometry. (Figure 4) These companies revolve around a digital inventory style, where they can supply manufactured parts on demand, alleviating the need to hold spare parts in reserve.
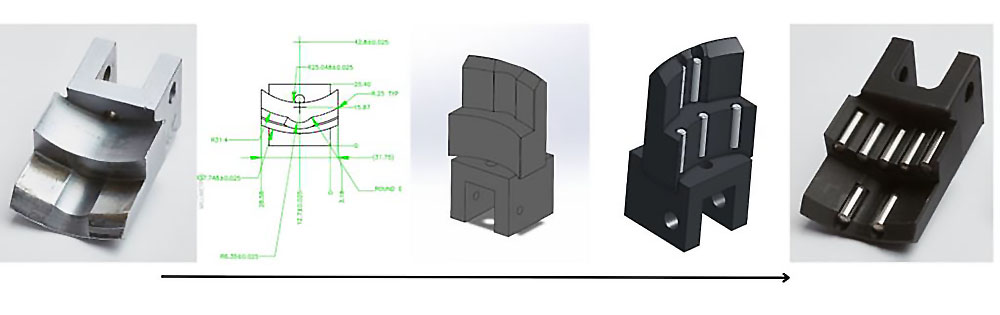
Parts on demand is a business model disruption to traditional supply chains, as it brings about a different perspective on inventory and repair. It means that suppliers can budget less space for the storage of spare parts. It also means that there is a change to the logistics of a service provider, making the supply chain shorter, and less complex. It allows companies to produce parts on demand, at the warehouse, eliminating the need to source a replacement part, and rely on the supply chain to receive the part. This perspective changes from utilizing existing external systems, and allows for the redistribution and structuring of manufactures to use an internal support structure. Print-on-demand manufacturing also serves as an additional revenue source for companies while supporting a manufacturing line. The proliferation of Industry 4.0—the Fourth Industrial Revolution characterized by a combination of automation and smart machines to create smart factories—is allowing the informed manufacturing process to produce products at high efficiency. This has led to a business model paradigm shift, moving from the selling of physicals products to selling products with service. (Savolainen, J.; Addit. Manuf. 2020) Today, small, localized and data-driven factories with resources can produce on-demand parts, rather than large factories, where massive amounts of time and money are poured into a single mold/tool, and these resources can now be spent elsewhere. This means that business both large and small have to rethink the type of model that they are following, whether it be a mass customization, mass variety, mass segmentation, mass modularization, mass complexity, mass standardization, or some hybrid model of all.
As Industry 4.0 transforms hardware companies into software companies, businesses will have greater flexibility to invest in learning while mitigating the ever-increasing burden of owning capital equipment. With software as the backbone, distributed and localized manufacturing will give companies added flexibility and agility and enable them to send 3D digital design files across secure networks to entire ecosystems of manufacturers.
For an example of the distributed manufacturing model in action, look no further than Automation Alley’s Project DIAMOnD, that recently linked 300 Macomb and Oakland County, Michigan manufacturers to make tourniquet parts to save lives in Ukraine.
As business models shift to incorporate 3D printing, questions are arising about intellectual property and the right to print anything mindset. The hobbyist community greatly embraces this, with repositories of models that are shared and uploaded. Additionally, there are many tools that allow for the reverse engineering of a designed part, in order to reproduce and fabricate. The question that may occur is, who retains the IP and how does the industrial segment maintain this? For instances, with OEM, will they share models for a specific part, if required to print on demand, or are other licensing schemes necessary as manufacturing shifts? We may also see a change in the government taxation model here. If inventories become more digital, how is a component taxed? Will it be based on the model produced or will it be based on the file stored? This is an unknown arena that is yet to be explored in great detail.
As more businesses begin embracing and implementing additive manufacturing, there will be a transition to a digital inventory and a digital twin model. A digital twin is a virtual model that accurately reflects a physical model, or a system. (Figure 5) This twin can be as complicated or as simple as you like, based on the amount of data utilized to build the model. The twin is built from input from an Internet of Things sensor, or real equipment entered by a technician. The digital twin not only allows for the tracking of a product, but also simulation in the digital environment. The twin is a risk-free environment, and can allow for device optimization, with minimal risk during manufacturing. In 2021, the FDA awarded Siemens $1.78 million to showcase how digital twin technology can be used to improve medical device manufacturing. It is unclear where the FDA will land on regulations regarding additive, however, tracking a product over its lifecycle, and showcasing how a model or product changes throughout production is key, and it is thought that the FDA may start requiring such a certificate in the future. The latest guidance for additive manufacturing came from the FDA in 2017, where they outlined 31 pages of guidance. In December of 2021, a new discussion paper was issued, where public input was sought on 3D printing for point of care medical devices. Concurrently, the Siemens-FDA demo will be intriguing to follow, as this manufacturing breakthrough may shape the future of medical device manufacturing and the government regulations landscape.
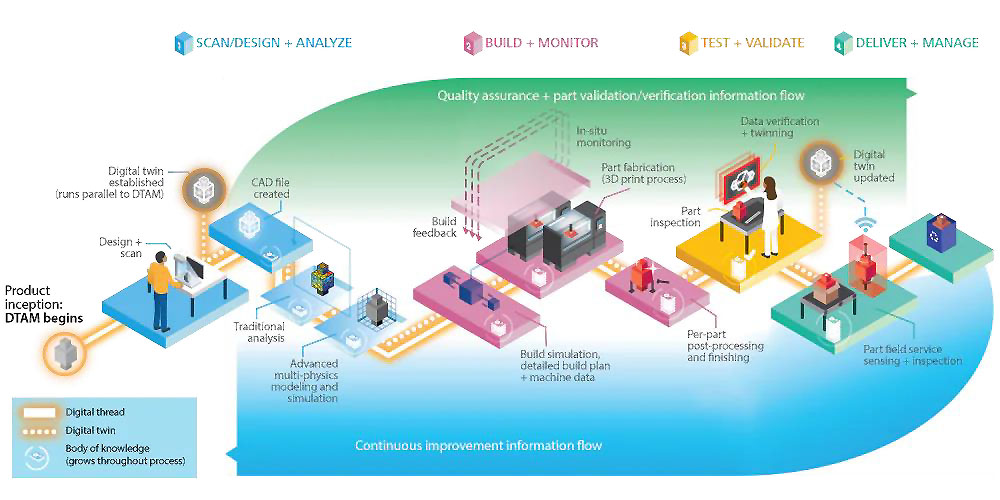
3. Digital Tools and Innovations
Additive manufacturing inherently is digital, and, as a result, requires new tools both physically and digitally to first ensure the quality of the part and then to analyze the part to ensure that the mechanical fidelity of the produced part meets specifications. Today, there are many types of systems that can be utilized for such analysis. As we seek more innovation, it is important to utilize the right tools, to ensure the fidelity of the produced part. Using computed tomography (CT), coordinate measurement systems and 3D optical scanning (for both defect detection and model accuracy determination) can be realized. (Figure 6) Using these tools, it is possible to look at both the internal and external microstructure and calculate the percentage deviation from the designed model, ensuring product specification. These scanning systems can also be incorporated into a digital twin, so that the product lifecycle and production can be tracked and further optimized. Scanning and inspections tools are agnostic and can be utilized on both metal and plastic produced parts. Another major advantage of an all-digital manufacturing platform is the ability to have online cameras with real-time defect detection. This allows a manufacture to pause a process and either abandon and restart the process, or adjust parameters to correct for errors. Lastly, analysis suites now exist for model comparison. Within these suites, a scanned model can be compared for deviations from the model, to ensure product tolerances. The full circle of manufacturing exists, where, in software, a model can be created, simulated for structure-strain and optimized. Then, the model can be produced as designed and optimized, scanned, and re-simulated, to ensure that the correct metrics are met.
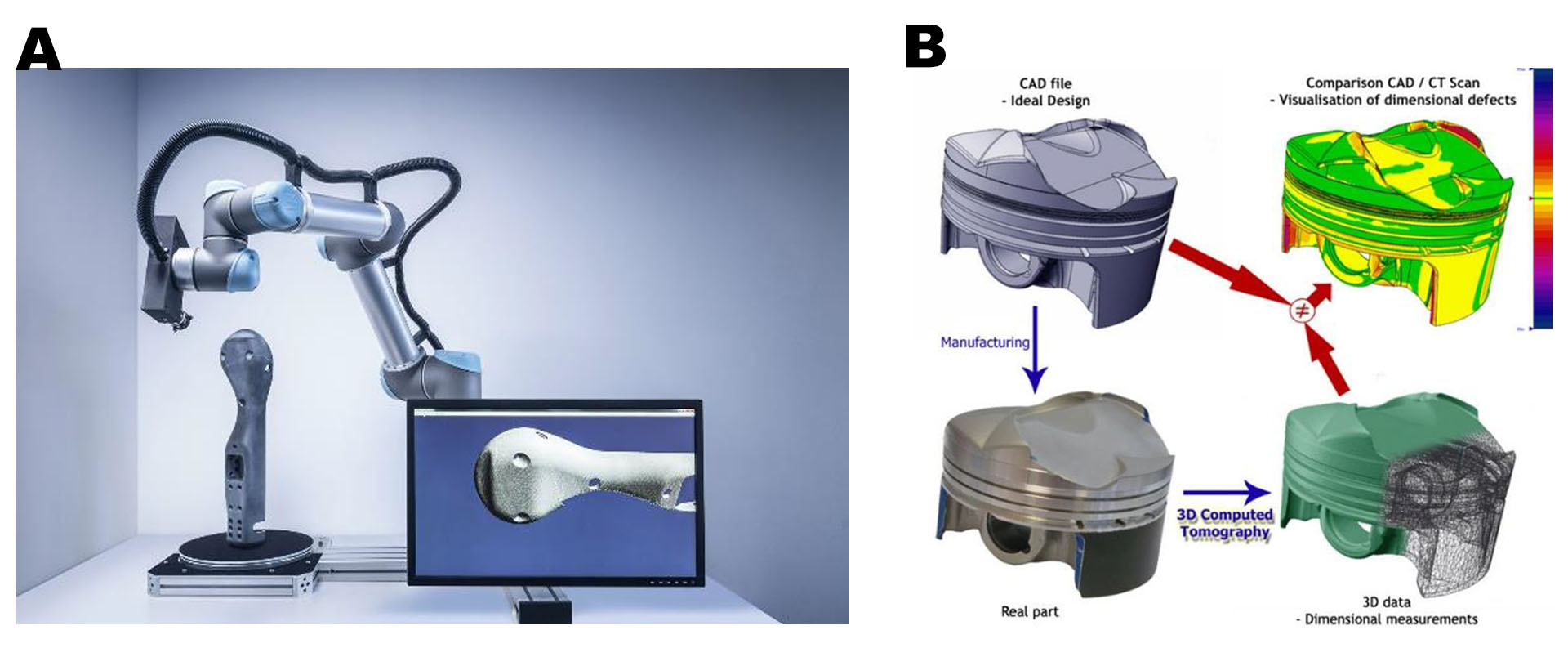
As sensors are integrated into additive manufacturing systems, a new pillar and frontier of 3D printing will be in situ monitoring of the manufacturing process and the ability to fix a detected defect in real time. Currently, commercially available camera systems, capable of real-time defect detection exist, however, they cannot repair a defect, but rather mark, pause or abandon the part. A key next step will be the ability to repair the defect once it occurs. Researchers have begun to utilize machine learning and neural networks to quickly process data for automated defects. A current challenge stems from the complexity and variability of the additive manufacturing environment. Take for instance a laser powder bed fusion system, compared with a fused filament deposition system, where parts are sintered, compared to extruded through a heated nozzle. As innovations occur here, researchers and manufactures will need to work together to find data processing and sensor systems that can be integrated together for each unique additive manufacturing technology in order to detect, repair and certify a part is produced to the designed tolerances.
It is worthwhile to note as well that President Joe Biden has announced an Additive Manufacturing Forward initiative to help increase U.S.-based suppliers to utilize additive manufacturing. Additionally, in recent years, government funding agencies such as NIST and ONR have increased the number of funding calls for scientific innovations to incorporate sensing systems with additive technologies. They aim to better understand the chemical mechanism of the fabrication process to better tailor and optimize the fabrication and understand the structure-function relationship of the additive manufacturing constructs.
Materials and systems are being further developed to maximize process controls and increase printing flexibility. Recently this year at RAPID-TCT, an additive manufacturing conference in Detroit, 6-axis printing systems were presented that can extrude continuous carbon fiber, combined with traditional fused filament fabrication. New systems that emphasized fiber reinforcement, systems that can serially print multiple parts simultaneously to increase part throughput, large format printers capable of printing life-sized objects, new liquid resin fabrication systems, and new metal 3D printing systems were also highlighted. Finally, software is enabling multicolor produced plastic parts and researchers are working on software for 6-axis robots that can print in unique directions to print in orientations that strengthen a part. As both software and hardware rapidly advance, it will be exciting to see how additive manufacturing is further improved to build parts that have enhanced chemical and mechanical properties that may just beat their traditionally produced counterparts.
In addition to these innovations, organizations like Fraunhofer USA are committed to accelerating new ideas through collaborative research projects with both industry and academic partners. Through the Global Fraunhofer network, there are teams with expertise in all aspects of additive manufacturing, including plastics, ceramics, metals and hybrid materials. In the past year, Fraunhofer USA has worked in collaboration with Fraunhofer-Gesellschaft to tackle several key challenges facing manufactures. For example, the organization looked at Ti-6Al-4V metal fused filament fabrication and how printing parameters can be correlated with densification during sintering. They also investigated how a construct deforms during a thermal de-binding process during the sintering run, and how AI can compensate for both gravity and shrinkage deformation during this process. (Figure 7A) During the sintering process, they investigated metallurgical properties of the constructs produced looking at the phase transition from sintering and annealing. They also researched increasing part complexity (Figure 7B), and what efforts would be needed to implement a digital twin and incorporate an online fused-filament-defect-detection system that can compare a model geometry with the printed construct. Lastly, they looked at the steps necessary to move fused filament fabrication from a 3-axis cartesian printing system towards a 6-axis robotic system, and how this can be integrated into a portable manufacturing system, comparable to manufacturing in a pod. (Figure 7C)
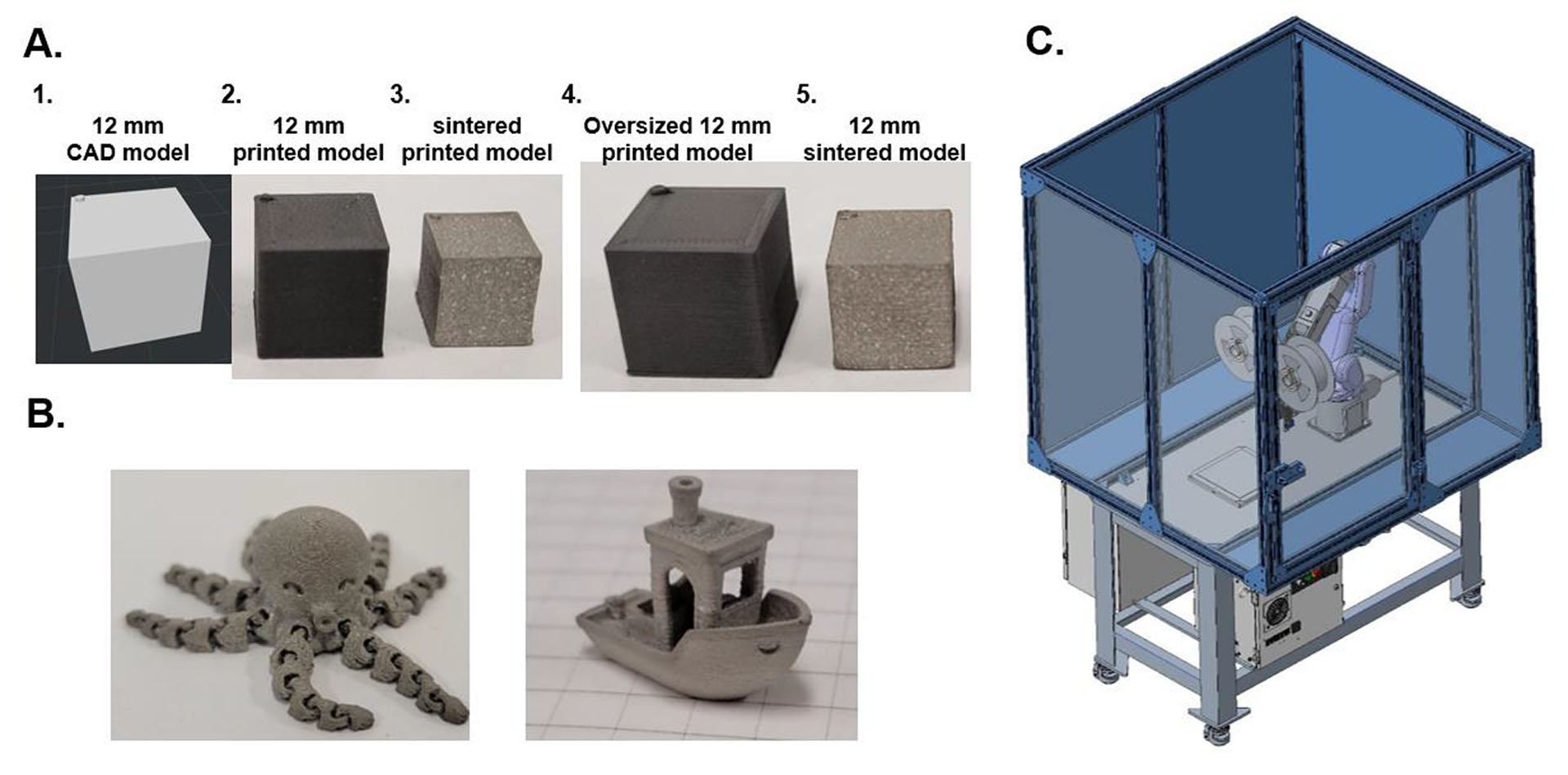
4. Next Steps
As 3D printing continues to mature and improve as a technology, we are seeing a paradigm shift in production as the consumer market demands customizability. Additive manufacturing enables the unique characterization and customizability that traditional manufacturing technologies lack due to the time constraints and costs associated with production. Additionally, additive manufacturing allows for new solutions, through the realization of a complex design that uniquely solves an engineering design previously not accessible. It is important to change how we look at additive manufacturing, and view it as a tangential tool, and to invest in digital inventory and flexible accessibility that it can offer. Through additive manufacturing new boundaries will be pushed, and we will continue to move towards an integrated and customizable world with limitless production capabilities. Below, the following table summarizes several key considerations discussed as a way forward in the adoption of additive manufacturing technologies.
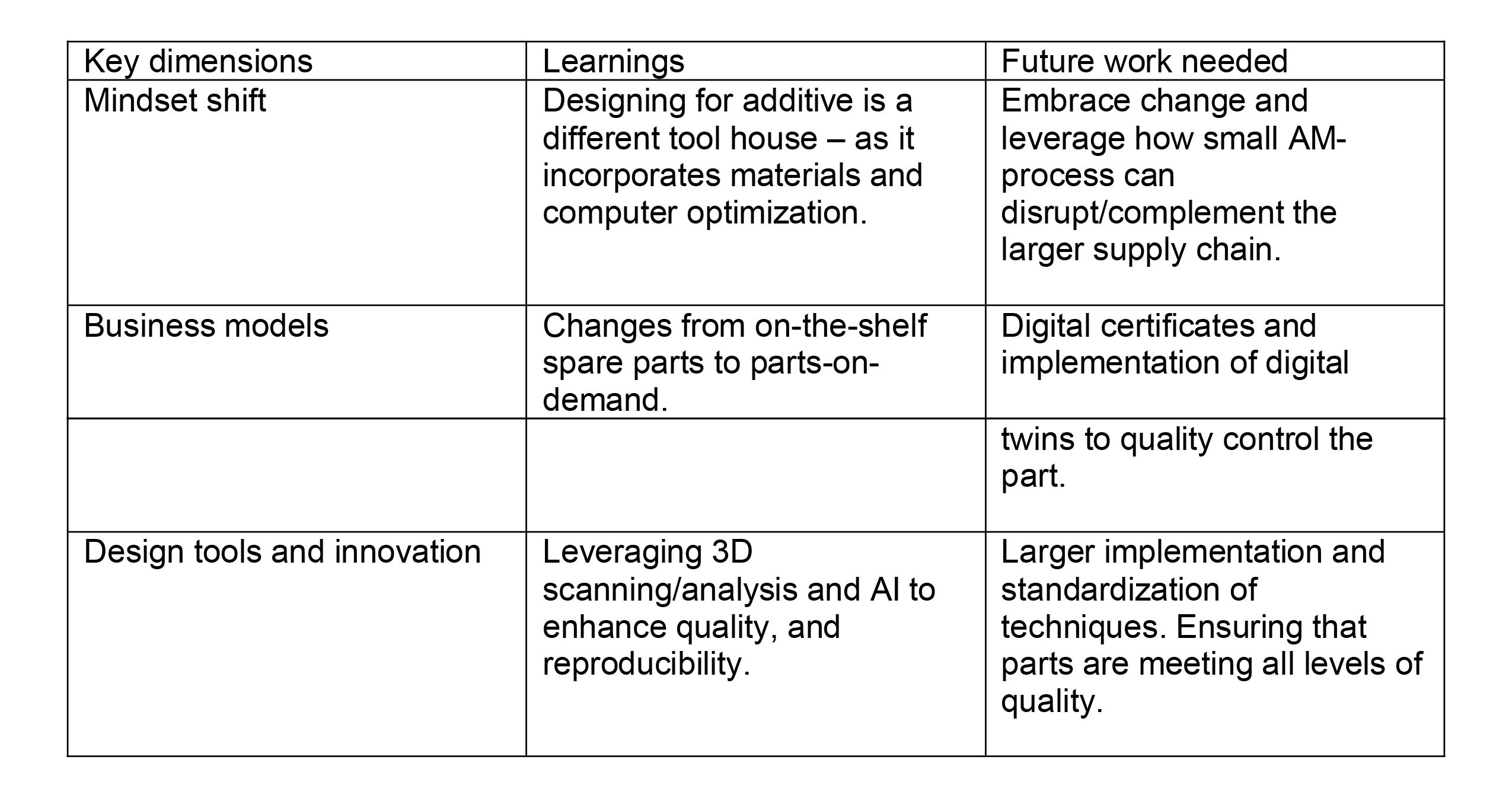